If you had to pick the most impactful manufacturing businesses shaping the world right now, which would you choose? Here’s a hint: these industries put the cars on our roads and the gadgets in our pockets. The automotive and electronics sectors don’t just lead by size—they drive technological shifts, economic growth, and jobs worldwide. It’s hard to look at the modern skyline, city streets, and living rooms without finding their fingerprints. Even in Birmingham, home to bustling car factories and electronics logistics hubs, their presence is obvious. The race to build faster cars and smarter tech isn’t slowing down. Let’s dig into why the automotive and electronics industries have claimed—and kept—their top spots, and what budding manufacturers can learn from their relentless march forward.
Automotive Manufacturing: Where Innovation Never Stops
Stroll past a car dealership or peek under the bonnet of your neighbour’s electric vehicle, and it's clear that automotive manufacturing isn’t what it used to be. The sector started with horsepower and steel and now buzzes with EV batteries and self-driving software. In terms of economic punch, the global automotive industry hit nearly $3 trillion in annual revenue by 2024. That’s not just from cars—buses, trucks, motorcycles, and a web of suppliers all count too.
Car manufacturing means more than assembling shiny prestige sedans. The scale is jaw-dropping: more than 92 million vehicles rolled off world assembly lines in 2023. Every single car pounds through hundreds of processes: stamping, welding, painting, and meticulous assembly. Even a 'simple' family hatchback like the Ford Fiesta draws on thousands of suppliers, each specializing in parts from microchips to mirrors.
Tech innovation is mandatory, not optional, in this business. Four years ago, electric vehicles were still mostly niche in the UK. Now, they make up about one in four new registrations. By 2030, many countries including Britain will ban new petrol-only cars. Hybrid and electric manufacturers like Tesla and BYD are upending an industry once ruled by old-school names like Ford, Toyota, and BMW. Want to see tech’s power? The latest BMWs have more coding lines than early NASA shuttles. Car makers have essentially become software companies dragged, sometimes kicking, into the digital age.
Beyond just production, automotive companies wrestle with a tangled supply chain. The 2021-2022 chip shortage made headlines as manufacturers lost hundreds of billions—not for lack of steel, but because inexpensive chips controlling window motors went missing. Lessons learned: manufacturers are now investing in vertical integration and supply chain security, making chip deals and even opening their own semiconductor plants.
Environmental pressure is reshaping how manufacturers operate. ‘Green’ isn’t just a buzzword; regulatory expectations force efficiency in both emissions and production waste. Techniques like lean manufacturing, automation, and 3D-printed parts are driving cost savings while shrinking carbon footprints. For anyone looking to break into automotive manufacturing, there’s space in every corner from retrofitting classic cars with electric motors to designing smarter assembly robots.
There’s a powerful jobs engine here. In the UK alone, automotive employs over 800,000 people, from factory machinists to logistics analysts, designers, and AI software engineers. Around the globe, the number shoots past 50 million across the supply chain. Entry can be daunting, but firms are hungry for new ideas—especially as software takes a front seat in every model year.
But money talks loudest. Profits in automotive aren’t just for the giants—suppliers building high-value niche parts, like battery modules and advanced sensors, can pull in impressive margins. Those thinking of starting up might find more success partnering as suppliers to established brands or focusing on aftermarket mods and services. Take a cue from the bits of kit people actually want: dash cams, telematics, charging accessories, and custom wheels. If you can solve a problem—like making electric van conversions easier for fleet operators–there’s real money on the table.
Stat | Figure |
---|---|
Global Auto Revenue (2024) | $2.9 Trillion |
Vehicles Produced Worldwide | 92 Million (2023) |
Jobs Supported (Worldwide) | 50+ Million |
UK New EV % (2024) | 24% |
Electronics Manufacturing: The Devices That Run Our Lives
Think about every screen you’ve touched today: phones, laptops, tablets, and the appliances at home. These wouldn’t exist without electronics manufacturing—and neither would the modern world. If you laid all the smartphones assembled last year end to end, you could circle the globe almost 20 times. The electronics sector smashed through $3.5 trillion in annual sales in 2024, making it one of the fastest-evolving industries anywhere.
Why the frenzy? Consumer demand never settles. Chip shortages recently hammered everyone from car companies to console makers, but also sparked a wave of innovation. Factories had to adapt, moving from Asia’s ‘Silicon Delta’ to new hubs in Vietnam, India, and even the UK, where big investments are landing in green tech, EV chargers, and medical electronics.
This sector is a wild mix of hardware assembly and cutting-edge science. One smartphone now packs more computing power than the computers used on the Apollo 11 mission. Devices get smaller, faster, and cheaper every year. Companies like Apple, Samsung, and Foxconn have perfected global supply chains so detailed that a delay in one Malaysian circuit board plant can send shockwaves to stores in Birmingham within days.
The pressure to keep up is relentless. Top electronics manufacturers are racing for the next big thing: AI-powered processors, ultra-thin flexible screens, sustainable packaging, and energy-saving chips. Take Apple’s annual launches—they’re more like global events than product rollouts. Behind the scenes, thousands of smaller manufacturers churn out components, from dust-sized capacitors to battery packs, that power this ecosystem.
Let’s not sugar-coat it: margins can be feisty, and counterfeit parts or supply hiccups bite hard. Yet, the sector is a magnet for both money and talent. In the UK, electronics manufacturing supports around 300,000 jobs, largely in high-value areas like aerospace, medical devices, and EV tech. Smaller firms have found real goldmines in ‘niche’ devices—think home smart meters, aircraft avionics, or medical wearables that track blood sugar in real time.
If you’re toying with starting up in electronics, specialization is the name of the game. The barriers to entry have dropped thanks to cheap prototyping services, but real wins come from tackling new applications: think Internet of Things devices, renewable energy inverters, or safety tech for factories. A bit of advice from seasoned pros—master design for manufacturing (DFM). A cool product is pointless if it’s a pain to assemble or source parts for. The sharpest newcomers build partnerships early with experienced manufacturers in the UK or Asia, keeping eyes peeled for compliance hurdles and eco rules. Sustainability is no longer a nice-to-have; recycled plastics and eco-packaging can set you apart and open new markets, especially across Europe.
Stat | Figure |
---|---|
Global Electronics Revenue (2024) | $3.5 Trillion |
Smartphones Produced (2023) | 1.5 Billion |
UK Electronics Jobs | 300,000 |
Average Chips Per Smartphone | Over 2,000 |
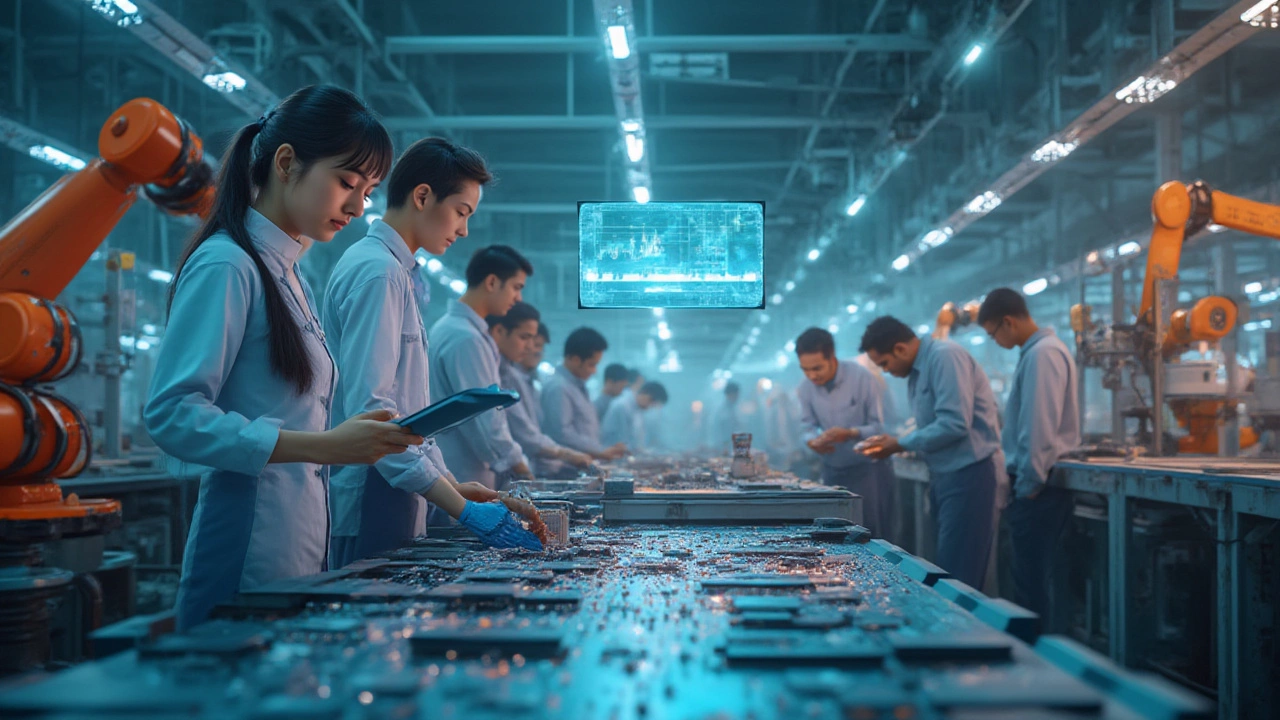
Why These Two? Unpacking Their Dominance
You might wonder why automotive and electronics manufacturing sit at the top, while textiles or food processing—both still huge—aren’t the headline makers. The answer is layered. First off, sheer market size. Both industries top out at trillions in global sales each year, dwarfing even the most successful fashion or food brands. But size alone doesn’t explain their influence.
The biggest edge is their role in powering other industries. Cars need semiconductors, batteries, advanced plastics—products rooted in electronics manufacturing. Electronics, on the other hand, are the “invisible engine” behind everything from renewable energy systems to medical equipment and the financial sector. The cross-pollination between automotive and electronics has created a self-reinforcing cycle: smarter cars demand smarter chips, while new gadgets drive demand for lighter, more efficient vehicles to deliver and support them.
Geopolitics gets a vote too. Major economies now see car and chip factories as strategic assets, throwing billions at local production. Take the EU’s “Chips Act” and America’s “Inflation Reduction Act” funneling subsidies into home-grown factories. Post-pandemic, governments have woken up to supply chain risks, especially for electronics. National priorities are set around strategic manufacturing muscle—think jobs, skilled migration, and security of supply. Both sectors are also magnets for research, spinning off innovations that ripple out to smaller manufacturing fields.
Diversification is another killer advantage. Auto makers now invest in robotics, digital services, and battery gigafactories, while electronics firms experiment with biotech, automation, and satellite tech. If one product line slumps, others cover the lost ground. This flexibility helps both industries withstand shocks, like recent wars or global health emergencies, better than more narrowly focused fields.
Speed and scale play their part. A typical car or phone model now has a refresh cycle of barely a year or two, ramping up competition and innovation. This means the next breakthrough—and the next business opportunity—could arrive any day. If you’re looking for a manufacturing business with staying power, agility, and big returns, these two sectors are in a league of their own.
Blueprints for Entrepreneurs and Operators
Okay, you’re inspired. But how do you get a foot in the door or supercharge your own operation? The first tip: study what the top dogs do, but don’t try to copy them exactly. Huge firms have vast resources, but you don’t need to be Samsung or BMW to find your niche in these industries.
Let’s break down a few tips:
- Find gaps: Success often comes from spotting what the big names miss. Think about supporting EV charging, recycling electronic scrap, or offering specialized firmware updates for medical devices. No market is too small if you can solve a real problem.
- Build relationships: Get tight with local suppliers and tech partners. Even giants depend on nimble small and mid-sized companies to adapt quickly to new tech and regulations.
- Keep a sharp eye on compliance: Manufacturing means playing by big rules—safety, environment, trade. Plan for this from day one.
- Invest in smart people: Hire for curiosity and adaptability, not just technical skills. The best teams can pivot as tech and tastes shift.
- Go green honestly: The market pays for real sustainability. Recycled components, energy efficiency, and ethical sourcing can turn heads globally.
- Lean on tech: Automation, smart data analysis, and online sales channels aren’t optional. Get familiar with the minimum tools—ERP systems, 3D printing, IoT dashboards—that keep even the smallest firms competitive.
- Start local, think global: Win your local market, but design with an eye on export or scaling up as you learn the ropes.
One example locally here in Birmingham? A small firm pivoted from assembling circuit boards for kitchen gadgets to designing battery systems for e-bikes. Another joined a supply consortium to develop EV chargers for home garages, unlocking deals across Europe when the UK market alone wasn’t enough.
Remember, you don’t have to be a full-stack manufacturer. Finding your speciality—say, firmware upgrades, quality inspection equipment, or localizations for regulations—lets you take a slice of a trillion-dollar pie without massive investment.
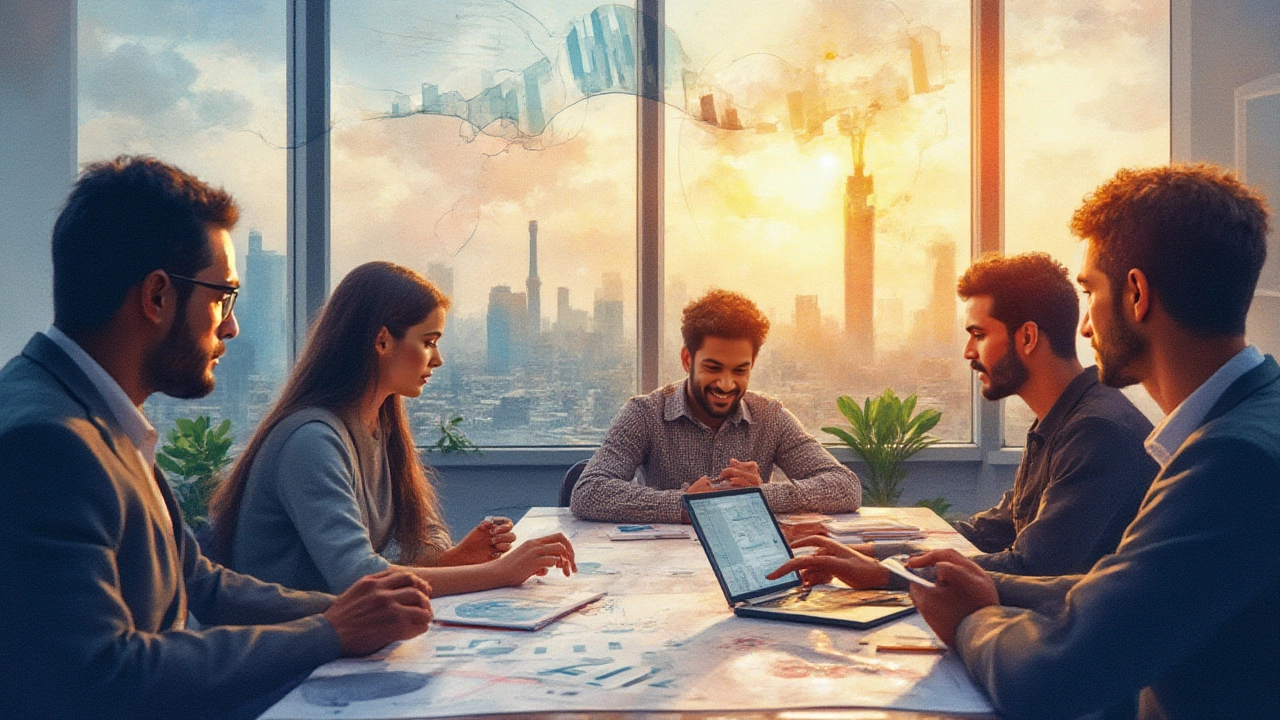
Tricks of the Trade: Keeping Up With Change
If there’s one certainty in the automotive and electronics industries, it’s relentless change. New standards, rising customer demands, and digital disruption mean yesterday’s best practice is today’s baseline. Staying ahead means investing in learning—formal education, online courses, or just relentless curiosity. Subscribe to the best trade journals, attend local trade expos like those in Birmingham’s NEC, and get involved in networks or associations.
Don’t be afraid of failure, but measure ruthlessly. Top manufacturers constantly experiment, tracking data to stop projects that drain cash and lean hard into what works. Even legacy firms now hire start-up veterans to inject speed and creative thinking into stodgy R&D labs. And increasingly, roles blur; a manufacturing job may mean programming robots or troubleshooting edge AI systems, not just handling machines.
Supply chain resilience also matters more than ever. Diversify your sourcing and keep emergency plans on deck for key components like chips or specialty steels. Stay awake to geopolitical swings—wars, tariffs, local labour unrest—and plan alternative shipping and procurement routes.
Then there’s customer engagement. Even in B2B, manufacturers can’t hide behind closed factory doors. Savvy companies use social media, community events, and transparent communication to build trust and draw in talent. Storytelling matters. Birmingham’s auto history, for example, is a badge of honour for workforce pride and draws investment—even as the industry evolves into something new.
Finally, never stop asking ‘what’s next?’ Challenge your assumptions about what can and should be made—and for whom. The road and the circuit board will look a little different every year, and staying alert is half the battle won.