Toyota, a name synonymous with reliability and innovation, has woven strong ties with Indian manufacturing for its engine production. This collaboration represents a significant fusion of global standards with local expertise. As one of the most prominent automobile manufacturers worldwide, Toyota's strategy in India is not only about meeting the high demand but also about leveraging India's unique strengths.
Delving into the dynamics of these manufacturing partnerships helps us understand how Toyota ensures high-quality standards while being cost-effective. It's fascinating to observe how this alliance plays a pivotal role in strengthening the local economy, providing jobs, and fostering skills development.
Moreover, there's a continual push towards technological advancement in engine manufacturing within India. The integration of cutting-edge technology and traditional manufacturing techniques illustrates how the industry is pivoting towards a more sustainable future.
This article will explore the pivotal role that local talent and innovative practices play in Toyota's operations, shedding light on a crucial segment of the automobile manufacturing industry in India. Join us as we journey through the exciting interplay between global automotive giants and local Indian prowess.
- Toyota's Indian Manufacturing Partnerships
- Impact on the Local Economy
- Technological Advancements in Engine Manufacturing
- Role of Indian Talent and Innovation
Toyota's Indian Manufacturing Partnerships
In the bustling landscape of India's automobile industry, Toyota engines stand out, thanks to the strategic alliances the company has forged with key Indian manufacturers. This partnership is not just a business arrangement; it is a convergence of cultures, technologies, and expertise. Toyota's collaboration with the Kirloskar Group has been pivotal, as Kirloskar has played an instrumental role in the production of engines, catering to both the domestic and international markets. The synergy between these two giants dates back to the late 1990s and has only grown stronger with time.
As the largest conglomerate in India's manufacturing scene, Kirloskar contributes significantly to ensuring that Toyota maintains its global reputation for quality and efficiency. Discussions around these partnerships often emphasize the meticulous attention to detail and the robust protocols that Toyota implements. An insider once mentioned, "In our journey with Toyota, the emphasis has always been on precision and innovation, leaving no room for error." This philosophy has propelled the collaboration to new heights, ensuring that the engines not only meet international standards but often exceed them.
Among the critical factors driving this partnership is the shared commitment to sustainability and technological advancement. Toyota and its Indian partners are constantly innovating their manufacturing processes, introducing green technologies and more efficient production methods. This includes endeavors like developing engines that are more fuel-efficient and emit fewer pollutants, aligning with global environmental goals. The partnership is also fostering a culture of continuous improvement and learning. Workshops, training programs, and knowledge transfer initiatives are regular, underscoring a commitment to nurturing talent that can drive the future of India's automobile industry.
It's remarkable to note the strategic importance of location in these partnerships. The factories, strategically positioned, ensure streamlined logistics and supply chain efficiencies. This strategic placement alongside a readily available skilled workforce makes India the perfect hub for Toyota's manufacturing ambitions. The infrastructure built around these facilities is designed to support high-volume production while being agile enough to adapt to new technologies and methods. This geographical and technical harmony exemplifies how Toyota's Indian manufacturing partnerships are a textbook case of strategic global-local collaboration.
"Our vision for India is not limited to production; it is about creating benchmarks in innovation and sustainability within the industry," said a spokesperson from Toyota at an industry summit.
The impact of Toyota's manufacturing partnerships goes beyond mere business; it's also about socio-economic development. These partnerships have generated thousands of jobs, contributing to skill development in the region. The clustering of ancillary industries around these manufacturing hubs has fueled a broader economic ecosystem, providing livelihoods and fostering entrepreneurship across the region. As India continues to emerge as a global manufacturing hub, Toyota's collaborative efforts play a crucial role in shaping this narrative, highlighting the transformative power of strategic alliances in the automobile sector.
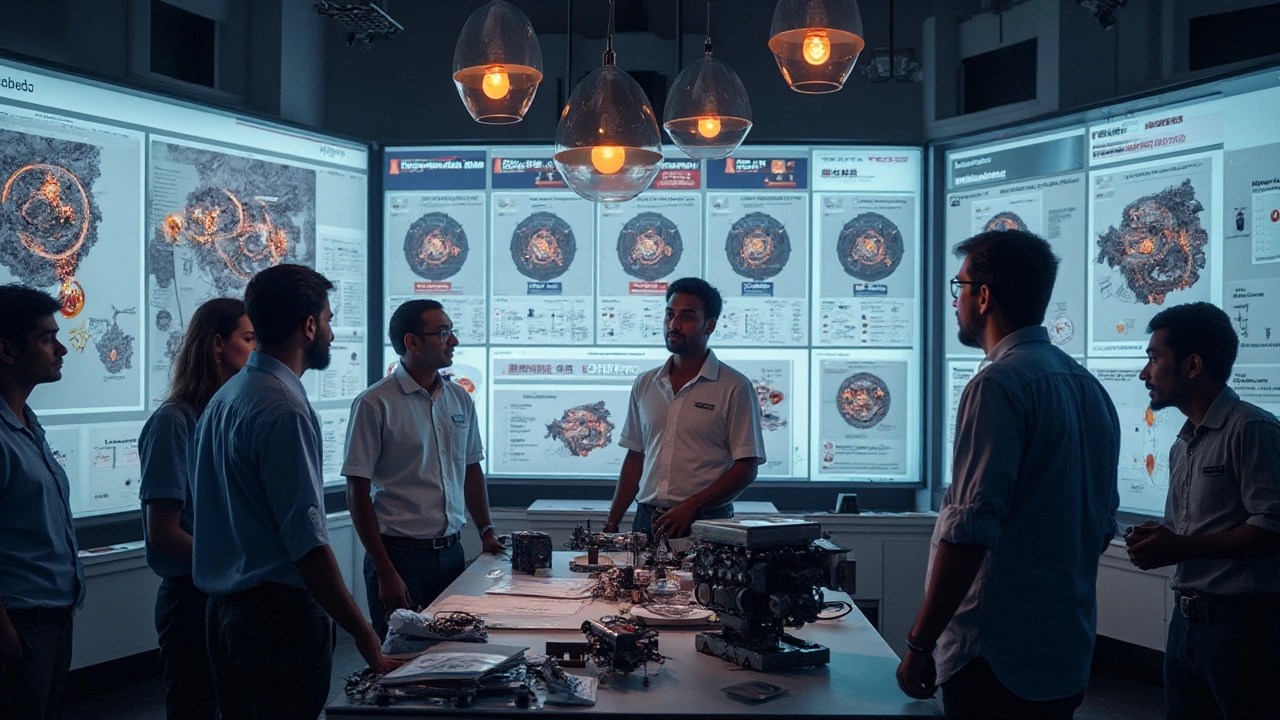
Impact on the Local Economy
The collaboration between Toyota and Indian manufacturers has ushered in a wave of economic changes that resonate throughout the country. Establishing engine production facilities not only boosts industrial outputs but also significantly elevates the livelihood of the workforce involved. It creates thousands of jobs directly in manufacturing plants and indirectly through ancillary industries. These opportunities are pivotal for younger generations seeking stable employment. They enable individuals to gain specialized skills that open doors to other professional realms. As more people enter the workforce, there is a ripple effect within the local economy, enhancing living standards and paving the way for thriving communities.
The strategic establishment of manufacturing plants in India leads to substantial investments in infrastructure development. Roads, power supplies, and logistics networks often undergo upgrades to accommodate industrial requirements, thereby improving accessibility and mobility for the surrounding regions. Such developments enhance the business ecosystem, attracting more national and international enterprises to set up operations, which in turn drives steady economic growth. This chain reaction of economic improvements highlights the critical role of automobile manufacturing in India's broader developmental landscape.
Moreover, the Indian government's initiatives to promote local manufacturing through programs like 'Make in India' have significantly aligned with Toyota's operational goals. By sourcing raw materials locally and utilizing domestic supply chains, these partnerships reduce dependency on imports, making the domestic automotive segment more resilient against global supply chain disruptions. Such practices not only bolster the national economy by increasing the Gross Domestic Product (GDP) but also diminish the trade deficit. A report by the Society of Indian Automobile Manufacturers (SIAM) indicated that the automotive sector contributes around 7.1% to India's GDP, illustrating the profound impact of such collaborations.
A noteworthy dimension of this collaboration is the nurturing of local talent and enhancing the skill set of the workforce. Through dedicated training programs and initiatives jointly spearheaded by Toyota and Indian counterparts, workers receive world-class training tailored to meet exceptional quality standards embodied by the Toyota brand. This systematic approach leads to a more robust, skilled labor pool that propels the industry towards excellence. In the words of a former Toyota executive,
"The true power of our partnership in India lies in the brilliant synergy between global expertise and the indomitable spirit of Indian workers."This capture of local energy and talent fosters innovation that transcends automotive manufacturing, influencing technological advancements and process efficiencies across various sectors.
Lastly, not to be overlooked is the environmental aspect. With enhanced production protocols and the adoption of eco-friendly processes, the environmental footprint of industrial activities in local regions experiences a reduction. The introduction of hybrid and cleaner engine technologies aligns with global sustainability goals and addresses local environmental concerns efficiently. Harnessing renewable energy sources for power needs within these plants further strengthens this commitment to sustainability. Thus, Toyota's engagement with Indian engine manufacturers is more than a commercial venture; it is an enabler of transformative economic, social, and environmental benefits that resonate on multiple levels.
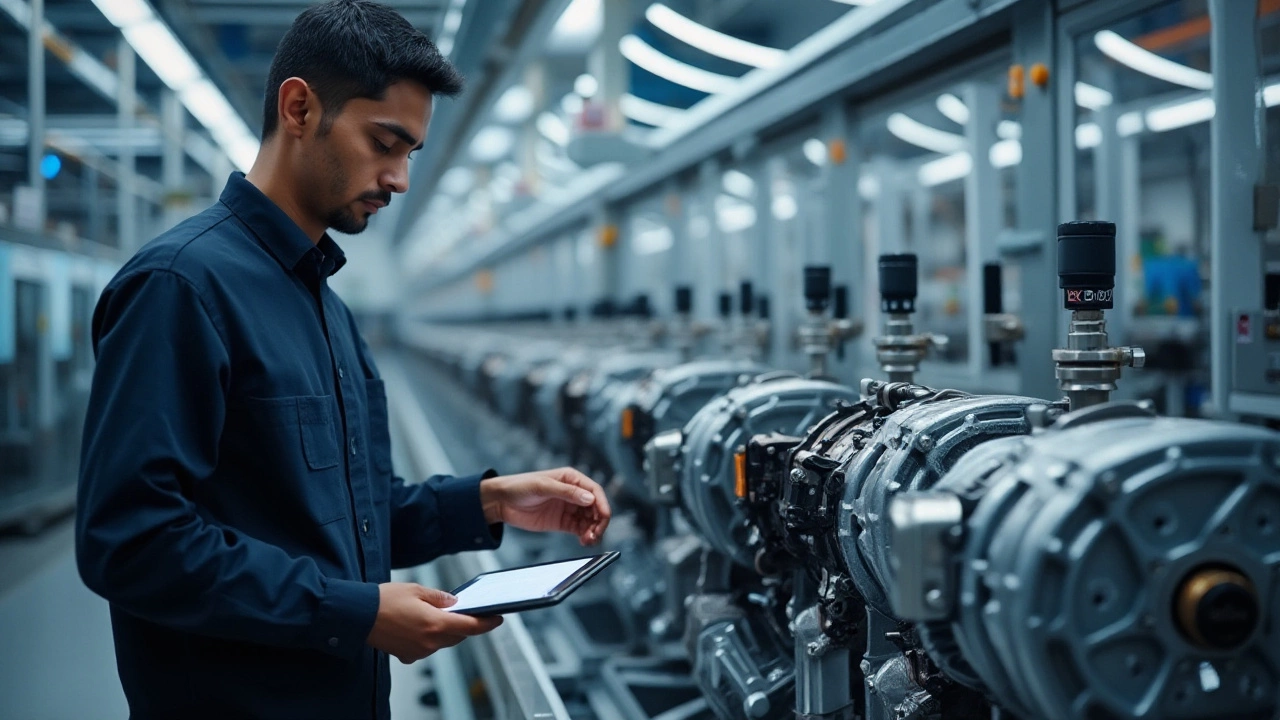
Technological Advancements in Engine Manufacturing
The automobile industry has been in a constant state of evolution, and the manufacturing of engines is at the heart of this transformation. In India, where Toyota has invested heavily in local production, technological advancements have played a critical role in propelling the industry forward. The quest for innovation underpins every stage of the engine manufacturing process, from the initial design to final assembly. The focus is not merely on producing effective powertrains but on crafting ones that are environmentally friendly, fuel-efficient, and rooted in cutting-edge engineering methods. These advancements are not just tailored to meet present-day demands but are also future-ready, anticipating changes in consumer preferences and regulatory landscapes.
One of the pioneering technologies adopted in recent times is the introduction of hybrid engine technology, which combines a traditional internal combustion engine with an electric motor. This technology is central to Toyota's sustainability mission globally, and its impact is being vividly felt in India as well. These hybrid engines reduce emissions, improve fuel efficiency, and deliver on performance. A deeper look into the assembly line reveals precision engineering powered by robotics, allowing for seamless integration of these technologies. Robotics ensures precision that human hands cannot replicate, and this elevation in manufacturing standards speaks volumes about the commitment to quality.
Digital twins represent another significant breakthrough currently being employed. By creating a virtual replica of the physical engine, engineers can run simulations and tests that forecast potential issues before they arise in real production lines. This preemptive problem-solving tool is invaluable, allowing for tweaks and changes without costly setbacks on the assembly floor. An engineer working with Toyota might quip that these digital twins are akin to having a 'crystal ball,' revealing faults before they manifest in reality. While it may sound futuristic, this technology is deeply embedded in the production processes of automobile engines in India today.
To further illustrate, consider the integration of IoT (Internet of Things) devices within the manufacturing setup. Sensors embedded in machinery relay real-time data to engineers, ensuring that every stage of engine production is monitored minutely. The analytics derived from IoT devices contribute to predictive maintenance, optimizing the efficiency of machinery and reducing downtime significantly. According to a recent industry report, incorporating IoT can enhance operational efficiency by up to 20%. This leap forward in technology ensures that the manufacturing process is not only efficient but also cost-effective, thereby benefiting consumers with better pricing and reliability.
The commitment to continuous improvement and innovation is further evidenced by Toyota's collaboration with renowned technological institutions in India. These partnerships not only encourage the adoption of new technologies but also foster an environment of research and development. They equip engineers with the latest tools to push the boundaries of what is possible in engine manufacturing. A study by a leading Indian university highlighted that innovation partnerships could accelerate the adoption of advanced technologies by a factor of three compared to isolated efforts.
The intersection of traditional manufacturing methods with modern technologies in India is redefining how engines are crafted for Toyota's diverse vehicle range. Through these technological advancements, the company not only meets the stringent requirements of the global market but also champions a greener planet. As we look forward to the evolution of engine manufacturing, Toyota's blueprint in India stands as a testament to how technology and human ingenuity can drive profound change in industrial landscapes.
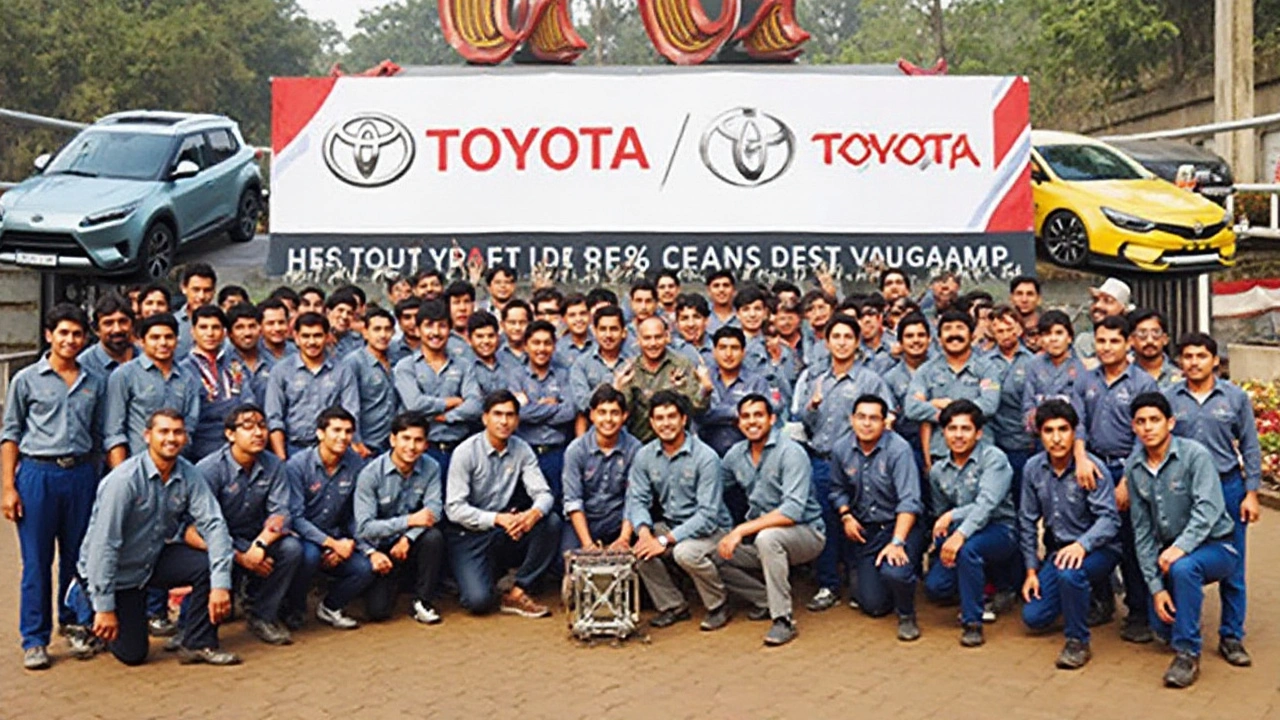
Role of Indian Talent and Innovation
In the dynamic world of automobile manufacturing, India's role has been growing steadily, particularly with industry giants like Toyota utilizing the vibrant pool of local talent and innovative mindsets. The availability of skilled engineers and technicians in India offers an invaluable resource for companies looking to combine cost-effectiveness with high-quality production standards. These professionals bring a blend of academic training and on-the-job innovation, allowing Toyota to adapt swiftly to changing market demands and technological breakthroughs. It's not just about manufacturing prowess; it's a symbiotic relationship where both parties continuously evolve and refine their techniques and approaches.
One cannot overlook the impact of various Indian Institutes of Technology (IITs) and others, which have been the breeding ground for some of the most brilliant minds in this field. Graduates from such prestigious institutions are known for their problem-solving capabilities, often pushing the envelope of what’s possible in engine manufacturing. These engineers are key players in conducting research, developing prototypes, and streamlining processes that can be scaled at a global level. Their input helps Toyota keep pace with the latest in engineering trends, sometimes even setting them, despite the competitive stakes.
The contribution of Indian talent extends beyond engineering to managerial roles in Toyota's Indian operations. The leadership often comprises individuals who blend an understanding of local cultural nuances with global business strategies. This makes them particularly effective in driving projects that require cross-functional collaboration and agility. Their initiatives often see the integration of start-up culture-driven quick iterative processes with meticulous planning, a hallmark of Japanese management practices.
Innovation is not confined solely to high levels of strategic planning. On the workshop floor, mechanics and machine operators frequently offer practical solutions based on firsthand experiences. They harness their deep-rooted understanding of the machinery to suggest alterations that could enhance efficiency or quality. These suggestions are frequently welcomed, considered, and, when feasible, implemented to great effect. This respectful engagement with the workforce not only improves the end product but also boosts morale and loyalty among workers.
The spirit of innovation also shows up in how Toyota in India is addressing sustainability challenges. The company employs numerous formerly labor-intensive processes with automated systems designed by Indian engineers. This shift has reduced the environmental impact significantly, aligning with Toyota’s global mission to reduce its carbon footprint. Through crucial adjustments in materials used and waste management processes, these local teams ensure all manufacturing aligns with rigorous environmental standards.
At times, Toyota India collaborates with local startups to incubate fresh ideas that may later be adopted in their mainline productions. These collaborations often focus on emerging technologies such as machine learning applications in vehicle diagnostics or AI-driven process optimization.
According to Mr. Suresh Cherian, a leading automotive expert and consultant, "It's incredible to watch how the synergy between tech startups and traditional manufacturing giants like Toyota can lead to groundbreaking innovations that benefit both the industry and the consumer."