If you’ve ever compared steel prices, you’ve probably scratched your head over how Chinese steel can be so cheap compared to US-made stuff. This isn’t just a small margin—sometimes we’re talking dollars per ton that really add up, whether you’re building a skyscraper or just running a fab shop.
This price difference can flip a whole project budget. It’s way more than just “labor is cheaper there”—that’s one of the biggest myths out there. From how China sources its iron ore to how their government props up the industry, the reasons stack up fast.
So, if you’re looking to buy steel or just want to know how the game really works, keep reading. Understanding why Chinese steel is so cheap isn’t just trivia—it’ll help you make better calls on sourcing, pricing, and planning the next time you need to cut steel costs without cutting corners.
- The Price Gap No One Can Ignore
- Raw Materials: Who Pays Less?
- Chinese Factories: Scale and Speed
- The Role of Government Support
- Why Labor Isn’t the Whole Story
- Tips for Steel Buyers
The Price Gap No One Can Ignore
The difference in steel prices between China and the US isn’t some technical hair-splitting—it's huge, and anyone in construction or manufacturing notices. For example, in early 2024, Chinese hot-rolled coil was selling for around $600 per metric ton, while the same Chinese steel product made in the US went for more than $1,000 per ton. That’s not a small change; it's a deal-breaker for a lot of projects.
Check out this quick comparison in the table below to get a feel for just how wide the gap is:
Year | Chinese Steel (Hot Rolled Coil, $/ton) | US Steel (Hot Rolled Coil, $/ton) |
---|---|---|
2023 | 670 | 1,190 |
2024 | 600 | 1,050 |
Now, multiply that gap by thousands of tons for a single project, and you’re suddenly talking millions of dollars in savings or extra costs. This price difference pushes a lot of US-based buyers to source from China, especially when profit margins are already tight.
But here’s the thing—it’s not just about the sticker price. Freight, tariffs, and logistics also come into play, but even with those, Chinese steel can still end up cheaper. That means for US steel manufacturers, competing is not just tough, it’s a whole different ballgame.
This gap is the reason you see debates about steel tariffs and “fair trade” almost every year. The stakes are high for jobs, profits, and which markets win big construction and manufacturing deals.
Raw Materials: Who Pays Less?
This is the heart of why Chinese steel ends up on the market for way less. China doesn’t just make a lot of steel—it buys resources smarter, too. One huge factor is just how much bargaining muscle China has. When you’re the biggest buyer of iron ore and coal in the world, you negotiate better deals. And they do.
China has locked in long-term supply contracts, mostly with Australia and Brazil. Big names like BHP and Vale push a ton of iron ore into the Chinese market every single day. In 2023 alone, China imported more than 1.1 billion tons of iron ore, which basically makes them the boss at the bargaining table. Plus, they run their own mines at home, which brings costs down even further.
Now, look at the numbers. Here’s a comparison for 2023 raw material costs per ton for steel manufacturers:
Country | Iron Ore ($/ton) | Coking Coal ($/ton) |
---|---|---|
China | 109 | 220 |
US | 134 | 260 |
You can see right away—Chinese mills pay less for pretty much every key input. Now throw in the fact that shipping bulk supplies into gigantic ports like Qingdao means lower logistics costs, and you’ve got another reason their numbers stay low.
US steel plants have to source some of their ore at higher prices and often haul it farther. On top of this, stricter environmental rules in the States mean added costs for how raw materials get mined and moved. All of this makes American steel less competitive right from the start.
So if you hear people say Chinese steel is cheaper just because of "cheap labor," you now know: raw material costs are the real game changer. That's why anyone buying Chinese steel cares a lot about the source story before worrying about labor savings or factory overhead.
Chinese Factories: Scale and Speed
When it comes to cranking out steel, no one does volume like China. Their advantage isn’t just about cheap raw materials; it’s about how massive and efficient their factories are. China produces more steel in a year than the next ten countries combined. In 2024, Chinese steelmakers pushed out over 1 billion tons, while US production hovered around just 80 million tons.
This Chinese steel juggernaut leans heavily on scale. Because Chinese plants are gigantic, they can run 24/7, spread fixed costs over more tons, and get better deals on bulk supplies. Not to mention, these mega-mills use newer and faster production lines. It takes way less time for a ton of steel to move from blast furnace to shipping container in China than in most American plants, especially older ones.
Just to put things in perspective, check out the real numbers:
Country | Total Steel Production (2024, Million Tons) | Number of Large Plants | Average Plant Age (Years) |
---|---|---|---|
China | 1,030 | Over 200 | 15 |
US | 80 | About 50 | 40 |
Modern equipment doesn’t just mean shiny buttons—it means faster turnarounds, less downtime, and lower costs per ton. Many Chinese mills were built or upgraded after 2010, while a lot of American plants are running on tech from the ’80s or earlier.
This scale makes it easier for Chinese factories to experiment with automation, energy-saving tech, and streamlined logistics. When you produce a billion tons, shaving just a fraction of a dollar off every ton saves a fortune. That’s how Chinese steelmakers can undercut prices globally, even before shipping costs or tariffs come into play.
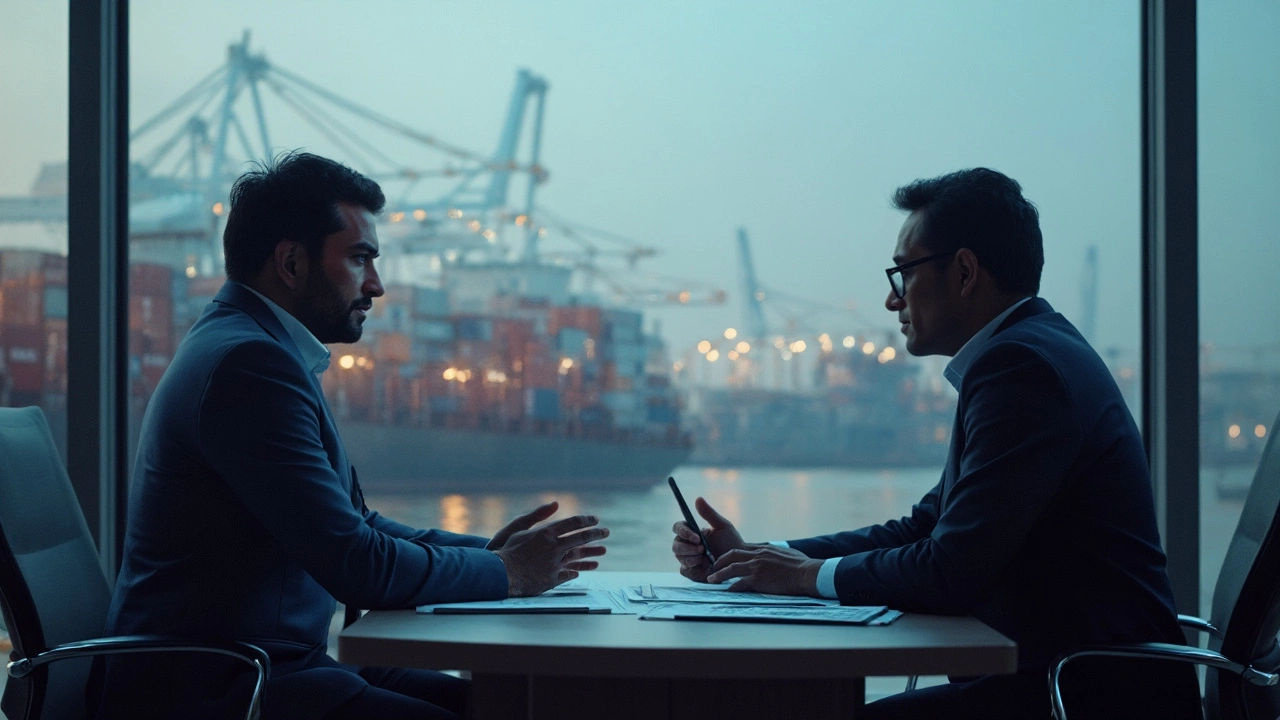
The Role of Government Support
When it comes to steel prices, the hand of the Chinese government is impossible to ignore. This is where things really tilt the playing field. The Chinese government has pumped billions into its steel industry over the years, and that’s not an exaggeration. Direct subsidies, cheap loans from state-owned banks, and special tax deals are all pretty much standard for large steel producers there.
Here’s a breakdown of what goes on:
- Chinese steel makers get easier access to financing since many big banks are owned by the government. Compare that to the US, where privately-owned mills deal with stricter credit terms and higher rates.
- Sometimes, provincial and local governments in China even cut land costs or energy prices just for steel plants. This directly reduces the overhead per ton of steel.
- Tariffs and export rebates encourage Chinese steel companies to export at lower prices and still make a profit. For years, this led to so much extra Chinese steel flooding international markets that the US and Europe slapped on anti-dumping duties just to compete.
- China has major state-driven plans to keep production high, which means mills can keep running even if domestic demand dips. That prevents shutdowns and keeps prices from shooting up.
These policies aren’t just rumors—every few years, international trade reports call out specific Chinese subsidies and call for action. For US plants trying to compete, this means they’re often up against an industry with both a cost and policy advantage. If you’re comparing bottom lines, government support is one of the biggest drivers behind that price advantage China has in the market.
Why Labor Isn’t the Whole Story
A lot of folks blame wages for why Chinese steel is easier on the wallet than American steel, but that’s just one piece of a way bigger puzzle. Sure, workers in China usually get paid less than those in the US, but labor actually only makes up about 10-15% of the total cost of making steel. That means the real savings come from somewhere else.
Take a look at this quick breakdown of cost drivers in steel manufacturing by percentage—it’s not just about paychecks:
Cost Driver | China (%) | US (%) |
---|---|---|
Raw Materials | 45-50 | 50-55 |
Energy | 20 | 22 |
Labor | 10-15 | 15-20 |
Logistics | 8 | 8 |
Other/Overheads | 12-17 | 10-15 |
See that raw materials row? That’s where you notice a bigger gap between the two. The Chinese steel industry has special deals and close ties to big suppliers, especially mines in Australia and Brazil. Plus, China keeps transportation and handling cheap and efficient. It’s not just what they pay their workers—it’s about what they pay for everything, and how fast they move it through the system.
Another major factor is the kind of tech and equipment used. Chinese plants are often massive, way bigger than what you see in the US, so they pump out more steel per shift with the same or even less labor input per ton. This scale means their overhead costs—everything from maintenance to management—get spread thinner over millions of tons each year.
- Chinese plants often use blast furnaces that run 24/7, cutting downtime and keeping output steady.
- More automation and newer equipment let them use labor smarter rather than just cheaper.
- Energy is handled differently too, sometimes with government discounts keeping costs low.
At the end of the day, wage costs matter, but they’re only part of why Chinese steel regularly undercuts US prices. If you’re buying or sourcing steel, don’t get stuck on labor rates alone—dig into how plants run and what kinds of deals they have on everything from power to raw ore.
Tips for Steel Buyers
Picking steel for your project isn’t just about the lowest sticker price. There’s a bit more to it, especially when you’re weighing Chinese steel against US-made options. It’s smart to dig into the details before you cut the PO.
First, check quality certifications. Not all steel labeled “to spec” actually meets international standards like ASTM, EN, or JIS. Ask for mill test reports and request third-party inspections if the stakes are high. Counterfeit certs do show up, especially on big import orders.
Keep an eye on tariffs and shipping. The US has slapped heavy duties on certain Chinese steel products since 2018. These tariffs aren’t going away anytime soon, and they can double the landed cost overnight. Run the numbers including freight, customs, and potential import delays. Suddenly, that “cheap” coil from China might not save you anything.
Lead times matter. Even if Chinese steel is in stock, shipping it across the Pacific can add weeks—or months if the ports get jammed up. US steel may cost more, but if time is money for your project, local mills can save you a headache.
Consider supply risk. China produces half the world’s steel, but it doesn’t mean supply is bulletproof. Sometimes, the Chinese government limits exports to control prices or hit climate targets. Unexpected quotas or energy curbs can turn a cheaper order into a missed deadline fast.
If you do go with Chinese steel, try to partner with an experienced importer or broker. They know what paperwork ticks the customs boxes, can help avoid sketchy suppliers, and stay updated on shifting rules.
- Double-check country-of-origin and test reports
- Calculate all-in costs (tariffs, shipping, warehousing, customs fees)
- Ask about recent supply chain delays before locking in ship dates
- If quality is non-negotiable, stick with trusted US or EU mills
- Build good relationships with your suppliers—straight talk saves headaches
The global steel game moves fast. Prices, rules, and risks can shift overnight. Staying alert and asking the right questions keeps your project on track and your budget in the black.