The year 2025 marks an exciting transition for the manufacturing industry, heralding new opportunities and emerging trends that promise to reshape the landscape. With a surge in consumer awareness about environmental issues and the rapid advancement of technology, businesses have unprecedented access to innovative methods that were only dreams a decade ago.
Entrepreneurs and investors are paying close attention to sectors such as green manufacturing and smart factories, which leverage automation to create efficient, eco-friendly processes. Developing sustainable packaging solutions and diving into the realm of 3D printing offer exciting avenues as well, with personal customization becoming a key market driver.
For those eager to navigate the changing tides of 2025, understanding these evolving opportunities is crucial. This exploration offers insights that could very well shape the future of the manufacturing world, and perhaps even seed the next generation of successful enterprises.
- Green Manufacturing
- Smart Factories and Automation
- Customization and Personalization
- 3D Printing Innovations
- Sustainable Packaging Solutions
Green Manufacturing
The demand for environmentally-friendly practices is at an all-time high in 2025, pushing manufacturing businesses to engage more deeply with sustainable methods. As the Earth faces mounting environmental challenges, the industry is under significant pressure—and rightly so—to reduce waste, minimize carbon footprints, and optimize energy efficiency. Enter green manufacturing, which not only aims to create more eco-friendly processes but also paves the way for innovative solutions that benefit both businesses and the planet. Companies that once viewed sustainability as a niche concept now see it as a necessity to address climate change and meet consumers' growing expectations.
Many businesses are now adopting renewable energy sources such as solar, wind, or hydroelectric power to run their facilities, drastically cutting their energy costs and contributing positively to the environment. The return on investment for these initiatives is remarkably favorable, as sustainable practices lead to greater operational efficiency and often qualify companies for various tax incentives and government grants. It's essential to understand that green manufacturing isn't just about using less energy; it also involves selecting sustainable raw materials, employing energy-efficient machinery, and optimizing logistics to reduce emissions. A turnaround in consumer behavior reflects a high preference for products that come with environmental certifications, pushing brands to integrate these aspects into their core policies.
"Sustainability is no longer about doing less harm. It’s about doing more good." — Jochen Zeitz, Co-Chair and former CEO of the B Team
Moreover, advanced technologies like IoT (Internet of Things) enable smart energy management. Equipped with sensors and analytics, manufacturers can monitor and manage energy consumption in real-time, ensuring that appliances and machines operate under optimal conditions. Predictive maintenance powered by AI and machine learning minimizes waste while improving operational lifespan and efficiency. In the realm of manufacturing, advancements in material science have also introduced new bio-based and recycled materials that are replacing traditional, less sustainable options. Such innovations not only contribute to a lower environmental impact but also often result in superior product performance.
The adoption of a circular economy model is another exciting development, rethinking the way resources and products are used, reused, and ultimately recycled. This approach dramatically extends the life cycle of materials by closing the loop on product lifecycles; businesses are encouraged to design for durability, reuse, and easy disassembly. Enhanced consumer awareness and clearer recycling schemes are guiding more companies to shift towards zero-landfill policies which have become a significant aspect of business ideas in today's landscape. Notably, the European Union projects a 30% resource efficiency gain by 2030 from circular practices—an enlightening statistic showcasing the tangible benefits of these strategies.
Smart Factories and Automation
The evolution of technology has revolutionized the way industries operate, and smart factories are at the forefront of this change. Utilizing the power of data and connectivity, these advanced manufacturing environments enhance production efficiency and reduce waste. In 2025, businesses investing in smart factory technologies will likely reap significant benefits by integrating automation with intelligent data analysis. This innovative approach not only streamlines processes but also leads to higher quality products.
Automation plays a pivotal role in the transformation of traditional manufacturing into the modern age. By incorporating robotics and machine learning, manufacturers can ensure precision and adaptability in real-time. For instance, predictive maintenance facilitated by IoT sensors allows for timely equipment repairs, minimizing downtime and enhancing efficiency. According to a study by the International Federation of Robotics, the adoption of industrial robots is anticipated to grow by 12% annually, underscoring the industry's shift towards automation.
Smart factories utilize a network of connected devices to monitor and optimize processes from start to finish. Data collected through IoT devices enables manufacturers to gain valuable insights into production patterns and energy consumption. This information can then be used to make informed decisions, improving both sustainability and cost-effectiveness. According to McKinsey, companies implementing data-driven practices outperform their peers by 23% on profitability, showcasing the economic advantage of embracing digitalization.
"The true potential of smart factories lies not just in the technology itself, but in the transformation of business operations that these innovations enable." - Deloitte Insights
The integration of advanced technologies such as AI and machine learning in smart factories guides the shift from reactive to proactive manufacturing strategies. AI-powered systems can predict demand fluctuations and adjust production schedules accordingly. This agility reduces overproduction and waste, aligning with the growing demand for sustainable practices. Moreover, these technologies support mass customization, allowing businesses to tailor products to specific customer needs without sacrificing efficiency.
Investing in smart factories is not merely a trend but a strategic imperative as global competition intensifies. Companies must evaluate their operations and develop a roadmap for incorporating smart technologies to stay ahead. This involves assessing current capabilities, identifying areas for improvement, and setting clear objectives. Collaboration across teams is crucial to ensure a cohesive approach that aligns with long-term business goals. With the continued advancements in technology, the journey to smart manufacturing is just beginning, offering endless possibilities for forward-thinking organizations ready to embrace change.
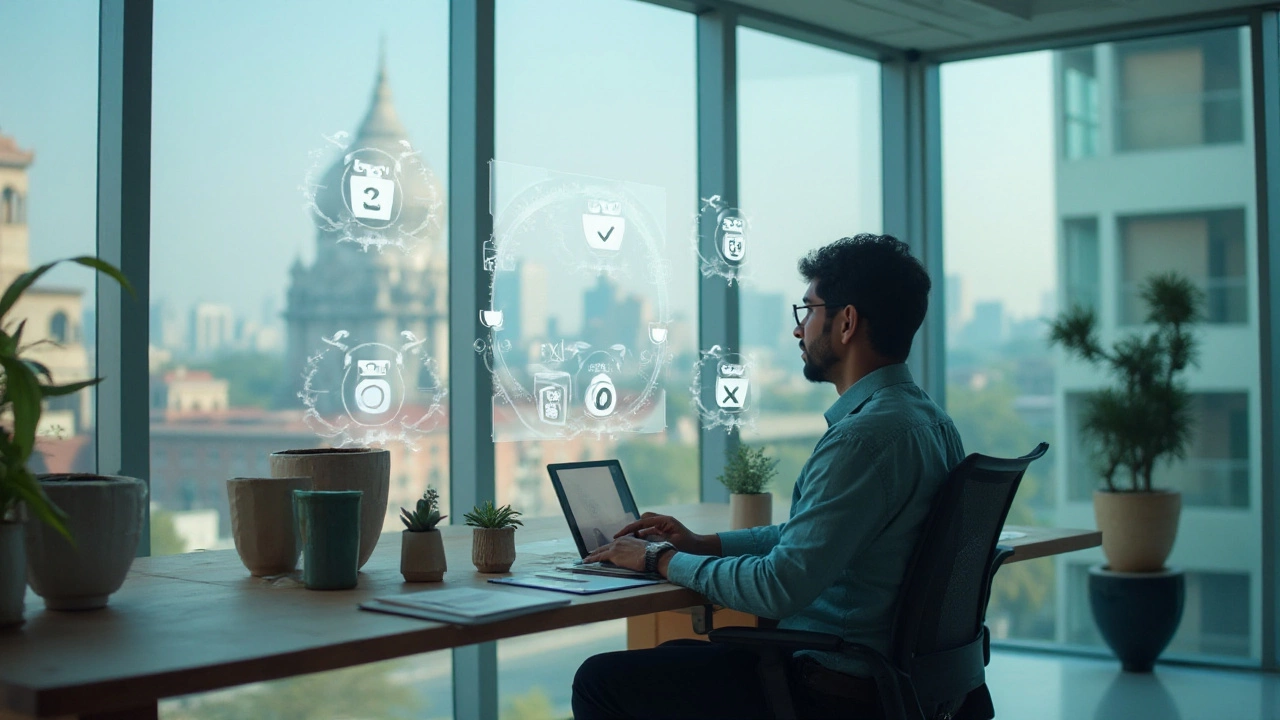
Customization and Personalization
In the realm of manufacturing, the trend of customization and personalization is rapidly gaining momentum, transforming once-static production lines into dynamic and adaptive systems. This shift is driven by consumers' growing desire for products that not only meet their functional needs but also resonate personally with their tastes, style, and values. As a result, companies that can successfully integrate personalization into their manufacturing processes are positioned to capture an eager market poised for personalized experiences.
One of the enabling technologies for this revolution is advanced software guided by real-time data analytics, which allows manufacturers to adjust their production in line with consumer preferences swiftly. These systems can handle a vast array of variables, ensuring that each product variant meets quality standards while still offering unique features. A prime example is the apparel industry, where consumers can design their own clothing by choosing colors, patterns, and even custom prints, making each purchase a personal statement.
In a recent discussion at a global manufacturing conference, a prominent industry leader remarked,
"In the new age of business, those who can offer a personal touch at scale will not just survive but thrive."His words highlight the impact of personalization as not just a trend, but a fundamental shift in customer expectations that businesses need to heed. By tapping into this demand, brands can foster deeper customer engagement and loyalty, translating into sustainable growth.
Moreover, the rise of 3D printing technology is paving the way for massively customized production. It allows for the creation of bespoke items without the need for large-scale retooling of machines or additional costs traditionally associated with short production runs. This technology's ability to produce one-off custom pieces economically brings a new level of materializing personalization into reality. For instance, jewelry designers utilize this technology to create intricate, tailored pieces that stand apart from mass-produced alternatives, offering customers a piece that truly feels their own.
Interestingly, data has shown that personalized products often command a premium price in the market. According to a study by Deloitte, over 50% of consumers are willing to pay more for personalized items, indicating that the investment in customization capabilities can yield considerable returns. As manufacturers continue to harness the power of customization, they will need to strike the right balance between personalization and the efficiencies of traditional manufacturing to unlock its true potential across various sectors. This is a pivotal year for embracing customization as both a strategic differentiator and a fundamental component of future-ready business models.
3D Printing Innovations
The onset of 2025 brings with it a renaissance in the realm of 3D printing, or additive manufacturing, as it's sometimes known in the industry. This technology, which builds three-dimensional objects from digital models layer by layer, is fast becoming a cornerstone in a myriad of sectors. Its capacity to enable rapid prototyping and customized production stands at the forefront, offering designers and manufacturers a flexibility that traditional methods simply cannot match. The versatility of 3D printing is especially captivating, empowering creators to go from concept to tangible product with unprecedented speed and efficiency.
In the past few years, the capabilities of 3D printers have skyrocketed, making them vital tools not just for hobbyists and small startups but for large industrial players who have begun to incorporate the technology at an astounding scale. Astonishing materials, from bio-compatible plastics to durable metals, are now within reach, broadening application possibilities. Industries like aerospace, healthcare, and automotive are already experiencing transformative shifts due to 3D printing's adaptability and precision. Indeed, General Electric’s adoption of this technology to manufacture fuel nozzles for their jet engines is a testament to its robustness and reliability in critical applications.
The environmental benefits are significant, too. With potentially zero waste, 3D printing cuts down on excess by using only the material necessary to create an object, minimizing industrial scraps. Coupled with the ability to produce locally, it contributes to reducing carbon footprints associated with transporting finished goods across long distances. And this plays right into the hands of sustainability-conscious businesses looking to attract eco-minded consumers.
Moreover, 3D printing is democratizing manufacturing, unlocking possibilities for smaller companies and entrepreneurs who can now enter the market without the enormous upfront costs traditionally required. This innovation is tearing down barriers to entry, allowing a fresh wave of smaller players to introduce creative solutions to the market. This accessibility could see a surge in bespoke, highly personalized products, catering to niche markets previously deemed unprofitable.
As the technology continues to expand and evolve, integrating artificial intelligence to streamline and optimize design processes, the scope of what can be created is virtually limitless. Companies are already exploring the use of recycled materials, opening up another avenue for sustainable production. With influential companies investing billions into the research and development of 3D printing technologies, the only certainty is that the sector is set to boom, redefining norms and setting new standards across the board. Anyone keen on capturing a slice of this burgeoning market needs to pay attention to this trend that is showing no signs of slowing down.
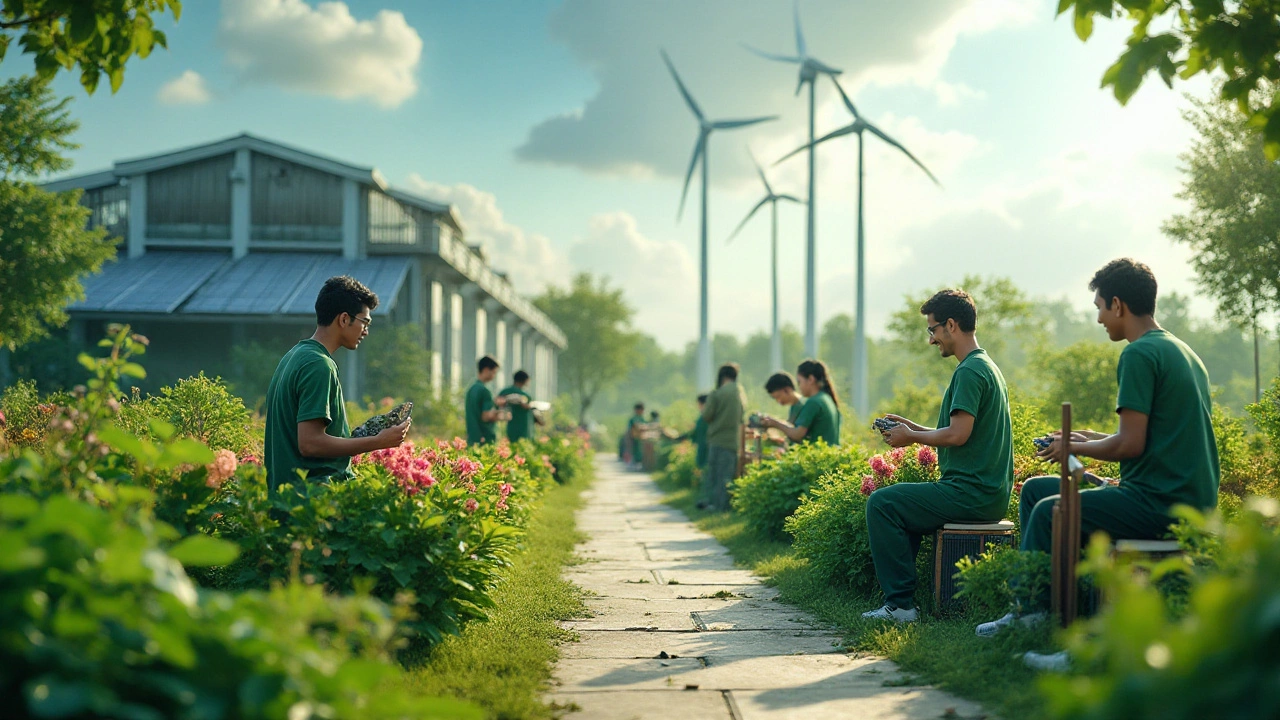
Sustainable Packaging Solutions
As we move deeper into 2025, the significance of sustainable packaging in the manufacturing sector cannot be overstated. The pressing demand for sustainable packaging solutions arises from consumers' growing awareness of environmental issues and their desire for eco-friendly products. This shift is encouraging manufacturers to innovate and adopt materials and processes that minimize environmental impact. Packaging innovations today are focused on reducing the carbon footprint, utilizing biodegradable materials, and implementing circular economy principles where possible. Beyond the consumer pressure, governmental regulations worldwide are enforcing stricter environmental standards, pushing companies to rethink their packaging strategies to ensure they meet compliance without compromising on the brand experience.
An interesting development in this sector is the adoption of materials derived from plant-based sources and the advocacy for eco-friendly designs. New materials, such as biodegradable plastics made from corn starch and packaging derived from waste products like agricultural byproducts, have shown significant potential. With innovation at the forefront, businesses are also considering edible packaging as a future possibility for food items, which could revolutionize the industry altogether. The shift to sustainable solutions is not just about material choices but also about reimagining the packaging lifecycle, including recycling and reuse strategies, to contribute to a zero-waste economy.
Cassie Lee, a renowned environmental scientist, notes, "Packaging is one of the most visible aspects of waste that consumers engage with, making sustainable transformations imperative for both ecological and economic reasons."
To cater to the market's needs, companies are increasingly investing in research and development to enhance the durability and functionality of sustainable materials. The rise of digital printing technology aids in reducing waste by enabling customization and demand-based production, thus aligning with personalization trends and consumer demands. Smart packaging technologies, including QR codes and sensors, are being integrated to provide informative labeling while minimizing the need for additional materials, thereby reflecting the smart factory principles of automation and sustainability.
Moreover, the economic viability of relocating production facilities closer to the market has started gaining traction, which means reduced transportation emissions and quicker response times to consumer demands. Encouragingly, partnerships across the supply chain are becoming more prominent as businesses collaborate to ensure that their packaging solutions are not only sustainable but also economically viable. This collaborative approach is pivotal as companies aim to share best practices and innovative solutions to tackle the challenging landscape of manufacturing.
Year | Global Adoption Rate of Sustainable Packaging |
---|---|
2022 | 42% |
2023 | 55% |
2024 | 63% |
2025 | 75% |
The future landscape of sustainable packaging is taking shape with increased emphasis on industry collaboration, technological advancement, and consumer interaction. The transformation journey is complex yet promising, with the potential to significantly reduce the environmental footprint of packaging solutions while meeting the needs of conscious consumers. As we envisage 2025 and beyond, these transformations in sustainable packaging offer a glimpse into a future where manufacturing not only supports economic growth but also adheres to environmental stewardship.