The ever-changing field of manufacturing is a fascinating battleground for some of the world's most influential companies. These industry titans are not just known for their massive output but also their foresight in adapting to technological shifts and market demands. In this article, we dive into the characteristics that make them leaders, how government policies are shaping their strategies, and what the future holds for the manufacturing industry.
Global manufacturing has often been influenced by local and international government schemes which aim to boost economies and encourage sustainable practices. Through strategic incentives and policies, countries have been able to elevate their manufacturing sectors to unprecedented heights. This interconnected relationship between government and industry paves the way for inspiring innovations and bold adaptations. As we explore this dynamic landscape, we'll uncover intriguing facts that highlight the industry's resilience and forward-thinking mindset.
- Pioneers in Global Manufacturing
- Impact of Government Schemes
- Innovation and Adaptation
- Sustainability and Ethical Practices
- Future Predictions and Trends
Pioneers in Global Manufacturing
The manufacturing landscape is dotted with giants that have set benchmarks in industrial capability and innovation. Among these leaders, a few names have consistently commanded attention. Take, for instance, China’s state-owned Sinopec, an exceptional example of how scale, government support, and integrated processes can cultivate industrial giants. Often listed among the top global manufacturers, Sinopec’s diverse operations cover everything from petrochemicals to refined oil products, marking its influence across a variety of sectors. The secret sauce of such companies does not merely lie in their geographical advantage, but in their ability to allocate resources efficiently, harness cutting-edge technology, and maintain strong governmental ties that fuel their expansive aspirations.
In the United States, companies like General Electric and 3M have continually redefined manufacturing by embedding innovation into their operational DNA. General Electric, with its focus on digital industrial capabilities, utilizes advanced analytics, artificial intelligence, and IoT technology to streamline production processes and deliver superior products. This strategy has not only enhanced operational efficiency but also allowed GE to adapt swiftly to changing market demands. As CEO Larry Culp once said,
"The impact of technology on manufacturing is a dawn of a new era, and only those who harness it will lead the future."
Another illustrion of manufacturing prowess is found in Germany with Siemens. Known for a rich history of engineering excellence, Siemens leverages automation and digitalization to remain a bastion of innovation in the manufacturing sphere. By aiming for Industry 4.0 standards, Siemens pushes the boundaries of what is possible in manufacturing, integrating smart technologies across its processes to deliver intelligent, efficient, and sustainable products. Their commitment to fostering an innovative ecosystem is matched by their dedication to sustainability, reflecting a broader industry trend towards environmentally conscious manufacturing.
Japan’s Toyota symbolizes a pioneering spirit with its legendary production system that has revolutionized automobile manufacturing. The Toyota Production System, emphasizing efficiency and waste reduction, has inspired countless others globally. As a leader in leveraging lean manufacturing techniques, Toyota continually invests in research, development, and process improvement. This ethos not only sets Toyota apart but encourages a culture that consistently seeks to improve quality, reduce costs, and increase operational efficiency, all crucial elements in the highly competitive automotive industry.
These pioneers, each with their unique strengths and strategies, illustrate the diverse approaches to success in the world of global manufacturing. Whether through state-backed support, technological adaptation, or sustainable practices, these companies show that excellence is not a one-size-fits-all but a tapestry of strategic maneuvers and resilient innovations.
Impact of Government Schemes
The influence of government schemes on the realm of global manufacturing cannot be overstated. Policies and initiatives crafted by governments worldwide have reshaped industries, driven innovation, and established pivotal global leaders in manufacturing. These schemes often aim to provide a competitive edge by leveraging technological advancements and encouraging sustainable practices. By setting such frameworks, governments grant companies the much-needed runway to expand their operations while maintaining ethical standards. Tax incentives, direct subsidies, and grants are among the tools frequently utilized to foster growth. A compelling example is China’s “Made in China 2025” initiative, which seeks to move the country up the value chain by encouraging companies to produce high-tech goods.
Besides initiatives encouraging domestic growth, international manufacturing also benefits from collaborative efforts among nations. Trade agreements, like the USMCA (previously NAFTA), have profound implications on manufacturing, allowing smoother transitions for goods across borders. These agreements reduce tariffs, thus lowering the costs associated with international trade, and allowing companies to invest in better technologies and innovation. Such collaborations showcase the immense potential governments have to reshape industries and bolster their capabilities. When speaking at a manufacturing summit, the late economist Paul Samuelson remarked, "Government policies don't just shape an industry's present, they write its future." With global manufacturing growing increasingly interconnected, the role of these policies becomes central to shaping the economies of the future.
Environmental sustainability also sees significant emphasis within government schemes. As climate change discussion takes center stage, initiatives like the European Green Deal aim to transform manufacturing practices by endorsing eco-friendly processes. To align with these directives, companies are encouraged to reduce carbon footprints while adapting innovative and energy-efficient technologies. The ripple effect of these policies creates an environment where manufacturing industries invest actively in research and development to meet the new standards, creating a cycle of continuous improvement and responsibility.
In an era where technological prowess defines success, schemes like Germany's Industry 4.0 initiative lay the groundwork for digital transformation within manufacturing. With a strong focus on integrating cyber-physical systems, the initiative encourages manufacturing entities to modernize through automation and digital technologies. The implications of such policies are vast, paving the way for industries to embrace artificial intelligence, the Internet of Things, and big data analytics, thereby enhancing efficiency and productivity. Governments play a pivotal role in providing the means for these transitions, ensuring that industries remain relevant and globally competitive.
The impact of these carefully curated government schemes often includes tangible metrics. For example, according to recent statistics, countries with active manufacturing incentives have witnessed an average increase in production output of 15% annually. In nations like Japan, manufacturing ventures backed by government-led research grants report up to 30% increases in technological upgrades. These statistics, while impressive, underscore the importance of strategic government intervention in shaping the future of manufacturing.
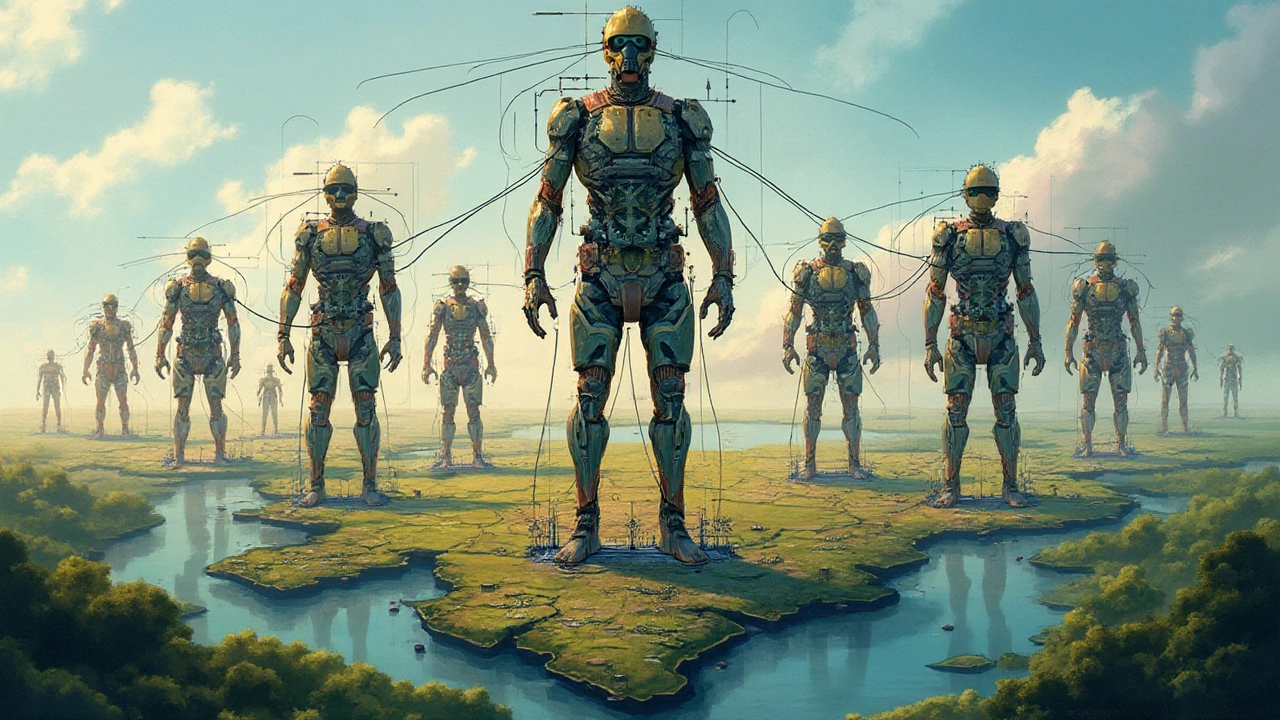
Innovation and Adaptation
In the fast-paced world of global manufacturing, innovation and adaptation stand as key pillars that sustain and fuel growth among industry leaders. Exploring the intricate dance between tradition and technology, manufacturing behemoths are not only integrating cutting-edge advancements but are also reshaping their operational landscapes entirely. For instance, the use of artificial intelligence has shifted from being just a visionary concept to a tangible asset. Factories now employ AI for predictive maintenance, allowing machines to alert their human counterparts before a malfunction occurs, thereby reducing downtime and saving millions.
One striking example includes Tesla, renowned for revolutionizing the electric vehicle industry. Tesla's Gigafactories employ sophisticated automation to streamline production processes, but it doesn't stop there. The level of adaptability they've demonstrated by integrating software updates into vehicle production is unparalleled in automotive history. It’s this nimbleness, combined with robust engineering, that keeps them ahead in the fierce competition. As Elon Musk once suggested, "If you're not evolving, you're stagnant." This statement captures the essence of staying inventive in manufacturing.
In addition to tech integration, the shift towards sustainable manufacturing has become inevitable. Giants like Unilever are paving the way by committing to sustainable sourcing and waste reduction, making strides toward environmentally-friendly production. Their adaptive strategies are not limited to environmental concerns; they also respond to consumer demands. This dual approach is crucial as cultural shifts and demands for corporate responsibility continuously reshape the industry landscape. As an added layer, government schemes often encourage such transformations by offering incentives for sustainable practices.
Adapting to local markets is another critical dimension of this section. Toyota’s success in global manufacturing can largely be attributed to its ability to tailor products to specific regional needs while maintaining consistent quality. This is achieved through adherence to rigid standards and an ability to innovate on a smaller scale, such as incorporating local materials or embracing regional design preferences. By balancing local adaptation with global efficiency, companies can maintain their competitive edge.
Embracing Digital Twins
Particularly interesting in the journey of industry insights is the concept of digital twins. These are virtual replicas of physical entities, enabling companies to simulate and predict processes in real-time. Siemens, known for its pioneering role in technology, has greatly benefited from digital twin applications. They harness this technology not just to optimize manufacturing lines but also to forecast potential issues, thereby significantly enhancing operational efficiency. This predictive capability exemplifies how technology can bridge the gap between theory and application.
Statistics from a recent industry survey highlight that around 57% of leading manufacturing firms reported a marked increase in efficiency due to implemented digital twin technologies. This illustrates the shift from traditional boundary-limited operations to dynamic, adaptable systems that are imperative in modern manufacturing.
From integrating sophisticated technologies to embracing sustainability, the global manufacturing scene is all about staying ahead through continuous innovation and nimble adaptation. This synergy is what keeps these titans thriving despite market fluctuations and shifts in demand.
Sustainability and Ethical Practices
In today’s world, sustainability and ethical practices have emerged as central themes in the manufacturing industry. The global shift towards eco-friendly and socially responsible manufacturing processes is not just an option; it's rapidly becoming a necessity. This green wave is driven by consumer demand for transparency, tougher regulations, and the pressing need to address climate change. Manufacturers across the globe are being pushed to reassess their production methods, minimize their carbon footprint, and adopt renewable energy sources. It's not uncommon to see companies boasting about the use of recycled materials, energy-efficient processes, and fair labor practices. These elements are now key indicators of a company’s commitment to sustainability and its role in building a better future.
The pressure is not solely external. Many manufacturing giants have embedded sustainability in their core business strategies, realizing it as a vital component of competitiveness and innovation. Take, for example, the efforts of industry leaders like Siemens and Honeywell, which have committed to carbon neutrality within the next few decades. Their strategies often include transitioning to circular economy models, where waste is repurposed, and resources are utilized more efficiently. Ethical practices in manufacturing go hand-in-hand with sustainability, focusing on fair wage, safe working conditions, and respect for human rights throughout supply chains. This holistic approach ensures that every step, from production to distribution, aligns with global ethical standards. One notable reflection of this trend is the increased participation in initiatives like the Science Based Targets initiative, which guides ambitious carbon reductions in line with climate science.
Government schemes and policies play a crucial role in incentivizing sustainable and ethical practices. For instance, the European Union’s Green Deal aims to make Europe the first climate-neutral continent by 2050, offering funding and support for businesses to innovate sustainably. On another front, China's Made in China 2025 initiative has sustainability at its core, encouraging manufacturers to incorporate green practices. These schemes often include tax incentives, grants, and educational programs that facilitate the ability for companies to transition smoothly into sustainable practices. It’s an intricate dance between government directives and industry execution, with both sides working towards a common goal. As India’s National Manufacturing Policy prioritizes sustainable practices, it’s clear that this is not just a Western narrative, but a universal commitment.
The benefits of integrating sustainability and ethical standards go beyond compliance and public image. Businesses that lead in these areas often gain a competitive edge, drawing in environmentally-conscious consumers and investors. They foster a culture of innovation and resilience capable of weathering disruptions, from resource scarcity to regulatory changes. For instance, Unilever, with its Sustainable Living Plan, reports that its sustainable brands grow faster compared to the rest of its portfolio. This kind of growth reflects the increasing consumer awareness and demand for responsibly manufactured products. These trends are supported by statistics showing that 81% of consumers worldwide feel strongly that companies should help improve the environment, as noted in a recent Nielsen report.
"Sustainability is no longer about doing less harm. It’s about doing more good." – Jochen Zeitz, Co-Founder of The B Team.
As we gaze into the future, the practices of today are setting the foundation for sustainable manufacturing. With technologies like AI and IoT, manufacturers are finding new ways to optimize energy use, reduce emissions, and eliminate waste. Moreover, the concept of Industry 4.0, centering on smart and autonomous systems fueled by data and machine learning, heralds an era where sustainability isn't just an initiative – it is an inherent feature of industry operations. These evolving standards offer a glimpse into a world where economic progress and environmental stewardship coexist in harmony, crafting manufacturing zones that are models of sustainable innovation. The challenge for manufacturers will be to break traditional molds without sacrificing growth, a balancing act that will define the next phase of global industrial development.
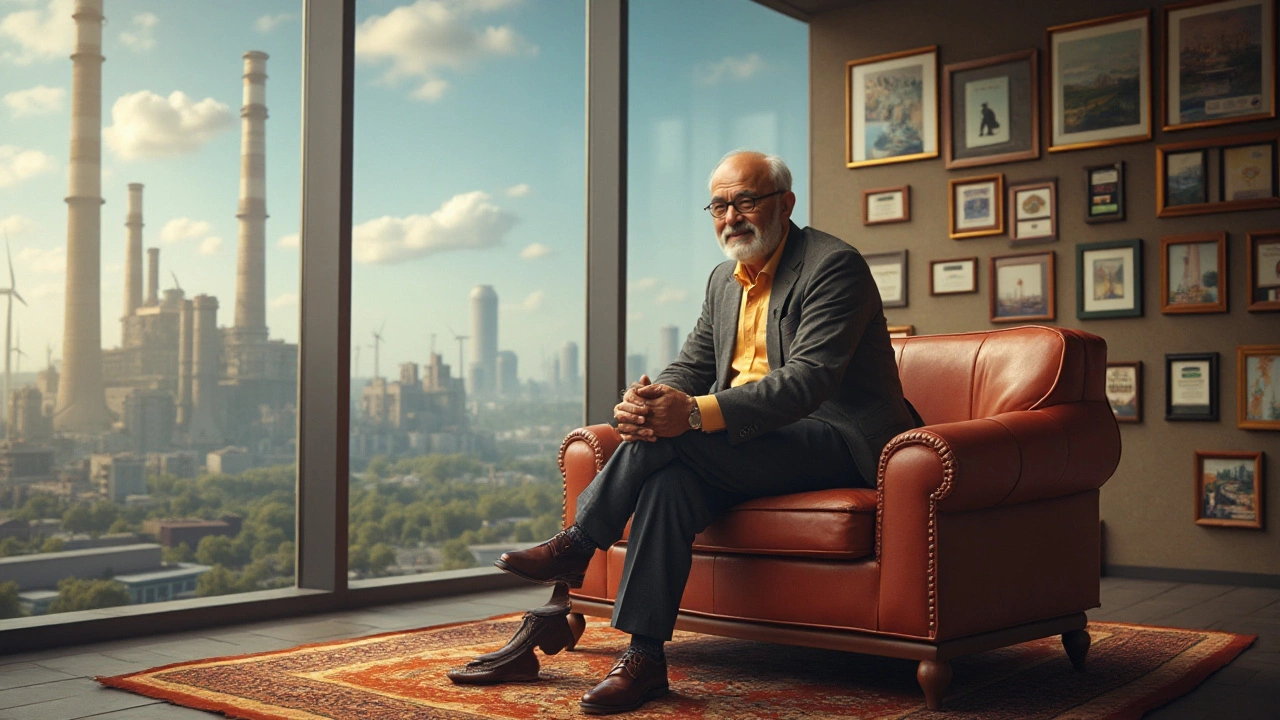
Future Predictions and Trends
As we stand on the brink of a new era in global manufacturing, there are several predictions and trends that are likely to define the future of this vast sector. One of the most significant shifts we can anticipate is the increasing integration of artificial intelligence and automation. These technologies are not just transforming production lines but are also reshaping the entire supply chain. With the capability to streamline operations, reduce errors, and enhance precision, AI is bound to play a pivotal role in future manufacturing processes. This shift towards automation is expected to create smarter factories where human oversight is minimal, and machine learning algorithms handle the decision-making processes traditionally managed by human operators.
There is an increasing demand for sustainable practices as environmental concerns become central to business strategies worldwide. Manufacturers are compelled to adopt eco-friendly practices, reduce waste, and utilize renewable energy sources. Governments are likely to introduce more stringent regulations in the coming years that encourage companies to comply with sustainability reports or risk heavy fines. These steps serve to push industry insights in a direction that harmonizes production needs with environmental stewardship. This is not merely a trend but a necessity, as both consumers and clients become more environmentally conscious and demanding a change in practices.
Embracing Digital Transformation
Another critical trend involves the digital transformation of manufacturing processes. The adoption of digital twins, IoT devices, and blockchain technologies are becoming instrumental in creating a seamless flow of information across various stages of production. The idea of a digital twin, a virtual replica of a physical product or process, allows for unprecedented insight, simulation, and optimization before actual implementation. IoT devices, connected and communicative, collect vast amounts of data that can enhance product quality, reduce downtime, and predict maintenance needs. Blockchain, on the other hand, provides a revolutionary approach to track and trace products from their point of origin to final destination, ensuring transparency and reducing fraud in the manufacturing supply chain.
"The manufacturing sector is stepping into a realm where embracing digital technologies is no longer optional but essential for survival," notes an industry expert in a recent report by the World Economic Forum.
In addition to these technological advancements, manufacturers must consider their workforce's evolving nature. With automation taking over routine tasks, the demand for highly skilled workers, particularly those adept in managing and interpreting data, will rise. This shift necessitates investments in workforce training and development programs to equip employees with the skills needed to thrive in an increasingly automated environment. Companies must prepare for a future where human and machine collaboration is not just ideal but commonplace.
Finally, geopolitical factors will continue to play a critical role in shaping the manufacturing leaders' decisions. Trade relationships, tariffs, and economic policies will significantly impact how and where products are manufactured. Diversification of supply chains to mitigate risks and reliance on single-source suppliers might lead to an uptick in regional manufacturing hubs. This decentralization may benefit nations with robust government schemes aimed at boosting local manufacturing capabilities, making them attractive candidates for future investments.