Setting up a small textile manufacturing unit in India is a venture that combines tradition with innovation. This endeavor requires a thorough understanding of several key financial aspects that influence its success. Whether you're an aspiring entrepreneur or an existing player in the textile sector, grasping the cost dynamics is crucial for strategic planning.
In India's culturally rich landscape, the textile industry stands as one of its pioneering sectors, robustly contributing to the economy. But what does it take financially to start a small textile factory here? From machinery and labor costs to deciphering government policies, navigating these waters demands a clear strategy.
This article breaks down the foundational costs associated with setting up a small factory in India, offering insights into what an investor should anticipate when entering this vibrant market.
- Initial Investment Considerations
- Cost of Machinery and Equipment
- Labor and Operational Expenses
- Location and Infrastructure Costs
- Government Schemes and Policies
Initial Investment Considerations
The journey of launching a small textile manufacturing unit in India begins with meticulous planning. Before you dive into this promising industry, understanding the initial investment scope is critical. The investment required hinges significantly on the scale of operations, the diversity of products you plan to manufacture, and the technology you choose to employ. Investing in a small factory often means screening through a series of choices that could ultimately shape the business trajectory yet keeping a personalized touch can truly make a difference.
One of the primary considerations is the choice of machinery and equipment. It typically demands the largest chunk of your financial outlay, especially if you're planning to incorporate advanced technology into your production line. The cost spectrum is broad, depending on whether you're setting up a facility for basic textile goods or opting for a more specialized production of fashion textiles. For instance, while a basic spinning machine might cost less, integrating additional equipment for processing and finishing could exponentially raise initial costs. It isn’t merely about filling the space with machinery; what matters equally is aligning this investment with a sensible return on investment strategy, which ensures each piece of equipment contributes to your output efficacy.
Another crucial factor is the investment in human resources. Hiring skilled labor not only boosts production efficiency but also necessitates a thoughtful budget allocation. With India’s vast pool of skilled and semi-skilled workforce in the textile sector, wages can vary widely based on location and skill level. It's also wise to consider training expenses to keep your workforce adept with the latest technologies. A well-trained team ensures lower operational risks and adds to the sustainability of your vision. Specific regions in India, such as Gujarat and Tamil Nadu, boast a rich heritage of textile prowess, potentially affecting labor costs due to regional expertise and availability.
Moreover, the location of your factory plays a pivotal role. Real estate and infrastructure costs in urban areas can be substantially higher. Urban settings, while offering better connectivity and logistics benefits, also escalate the investment as compared to rural setups where land may be cheaper but requires thoughtful logistics planning. These costs aren't just about purchasing or leasing space; they extend to the development of essential infrastructure like energy supply, water, and roads, which support your factory's operations.
"India’s textile industry is a significant contributor to its economy, not only in terms of output but also in terms of employment. It's essential for new entrepreneurs to understand the nuances of their initial investments for sustainable growth," remarked Dr. Arvind Panagariya, former Vice-Chairman of NITI Aayog.
Additionally, an often overlooked but vital aspect involves government schemes and financial incentives. The Indian government offers various schemes aimed at promoting the textile industry, particularly small and medium enterprises (SMEs). Familiarizing yourself with these can unlock substantial cost savings, from subsidies for certain types of machinery to tax rebates and duty drawbacks. India's textile sector enjoys considerable support, aimed at boosting exports and creating employment, and tapping into these benefits can significantly offset initial costs.
Understanding market trends is also indispensable. Market demands can fluctuate, and a well-researched approach in alignment with current and anticipated fashion trends can save costs and potentially produce high returns. Aligning your strategy with these trends ensures your products remain relevant and competitive in the market. Entrepreneurs should thus keep their fingers on the pulse of fashion, assessing consumer demands dynamically and adapting quickly.
Cost of Machinery and Equipment
When embarking on the journey to establish a small textile factory in India, the expenditure on machinery and equipment forms a significant portion of the initial investment. Understanding the types of machinery needed and their respective costs is crucial for effective budgeting. In textiles, machinery isn't just a one-time purchase but a long-term investment that affects your operational efficiency and product quality. Indian textile manufacturing requires equipment across various stages, from spinning and weaving to dyeing and finishing. Each stage demands specific machines that can range widely in cost, depending on brand, technology, and capacity.
For instance, a modern spinning machine, essential for transforming raw fibers into yarn, can start from approximately ₹20 lakh (around $24,000) for high-efficiency models, but prices can soar with advanced features. Weaving machines, crucial for producing fabrics, can vary from ₹10 lakh ($12,000) for simple models to upwards of ₹50 lakh ($60,000) for those with advanced automation capabilities. The choice between semi-automatic and fully automatic machinery significantly influences both cost and productivity. Weighing these factors carefully, alongside anticipated production volumes, will help in deciding the most cost-effective setup.
The dyeing process, a pivotal step in textile production, often demands expensive equipment due to the sophisticated technology required to ensure even color distribution and fastness. High-temperature dyeing machines might cost around ₹30 lakh ($36,000) or more, reflecting the advanced technology and materials involved. Investing in quality machinery is crucial not only for maintaining the standard of the output but also for minimizing waste and reducing environmental impact. It is important to note that while upfront costs might be higher for advanced machinery, the efficiency and reduced operational costs often balance out this investment over time, providing a competitive edge in the textile market.
Establishing relationships with reliable machinery suppliers can lead to potential savings and better service terms. Many Indian manufacturers offer leasing options, which can ease the initial financial load. Used equipment is also an option that some startups consider, though this comes with risks in terms of maintenance and energy efficiency. According to insights from the Indian Textile Equipment Manufacturers Association, "Investing in eco-friendly and energy-efficient machines may involve higher costs initially but significantly lower operational costs." Innovations in technology mean that textile machinery is continuously evolving, offering more options for scalable growth and sustainability, factors that are becoming increasingly important in the industry.
Machinery Type | Approximate Cost (INR) |
---|---|
Spinning Machine | ₹20 lakh - ₹50 lakh |
Weaving Machine | ₹10 lakh - ₹60 lakh |
Dyeing Machine | ₹30 lakh and above |
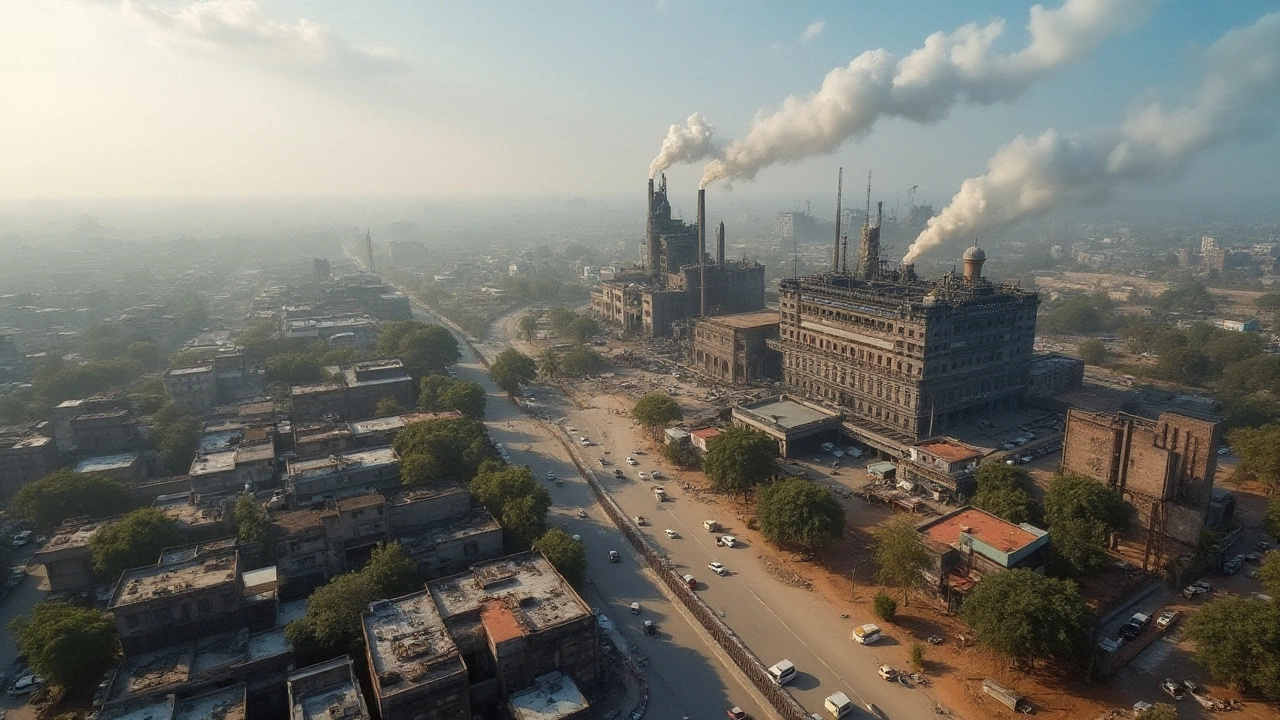
Labor and Operational Expenses
In the bustling world of textile manufacturing, labor and operational expenses form an integral part of the financial planning process. India, with its vast pool of skilled and semi-skilled workers, provides a fertile ground for textile entrepreneurs. However, understanding the nuances of labor laws and expenses is pivotal. Labor costs in India are significantly lower compared to Western countries, which is a major draw for investors. But don't be mistaken; skilled labor still demands competitive salaries. The textile sector, one of the largest employers in the country, is governed by specific labor laws ensuring fair wages and working conditions, which factory owners need to comply with.
Operational expenses extend far beyond just salaries. They encompass daily operations including utilities like electricity and water, which form a considerable percentage of running costs due to the energy-intensive nature of textile production. Efficient supply chain management also affects expenditure. Procuring raw materials efficiently, maintaining a seamless production line, and managing waste are crucial for keeping operational costs down. Embracing local suppliers can reduce transportation costs and fortify supply chains against disruptions.
Another nuance to consider is the potential for unforeseen expenses. Machine maintenance, insurance, and unexpected price hikes of raw materials can pose significant challenges if not anticipated well in advance. A smart entrepreneur should incorporate a cushion for such uncertainties within their budget.
"The textile sector in India is competitive, and cost management is crucial," says Manu Jagirdar, an industry expert. "It's the unseen expenses that tend to catch many off guard. Having a comprehensive understanding of operational expenses can make or break a successful textile venture."
Investments in employee training should not be overlooked. Empowering workers with skills related to new technologies can lead to an increase in productivity and quality. It's not merely about hiring; it's about creating a conducive environment where labor efficiency thrives, which paradoxically lowers costs in the long run. Training programs, often in collaboration with government initiatives, can be a boon for both workers and employers.
To give a clearer picture, here's a simple outline of typical operational expenses in a small textile factory:
- Workforce Wages: Including salaries, bonuses, and benefits.
- Utilities: Electricity, water, and other necessary utilities.
- Maintenance: Regular upkeep of machinery and infrastructure.
- Supply Chain Costs: Transportation and storage of raw materials.
- Compliance Costs: Ensuring adherence to labor laws and environmental norms.
By keeping a close eye on these expenses, textile manufacturers can create a sustainable and profitable business model. It is this meticulous attention to labor and operational intricacies that often differentiates the successful factories from those that struggle to stay afloat.
Location and Infrastructure Costs
When planning to set up a small textile manufacturing unit in India, choosing the right location is paramount. The cost, accessibility, logistics, and availability of raw materials heavily influence location choice, requiring careful consideration. Urban areas like Mumbai and Delhi boast robust infrastructure and connectivity, but come with higher real estate prices, impacting the financial outlay significantly. On the other hand, states like Tamil Nadu and Gujarat offer textile clusters, where costs might be lower while still providing access to skilled labor and established markets.
The infrastructure costs include not just building or renting factory space, but also the development required for utilities such as electricity, water, and waste management systems. This step is essential, as efficient operations hinge on these basic amenities. In regions where the textile industry flourishes, the state governments may offer tax incentives or subsidies on electricity, directly easing operational expenses. These benefits can drastically reduce the burden on new manufacturing units and enhance competitive advantage.
Setting budget expectations for different locations involves benchmarking against existing units and evaluating the potential for growth. If production aims for export, proximity to ports and international cargo hubs like Chennai or Mumbai could affect logistical costs and ease of operation positively. Balancing location and infrastructure costs against potential profitability and market access becomes a strategic necessity.
In addition, the integration of modern technology in infrastructure affects initial costs but may lead to long-term savings. Technological upgrades in logistics and inventory management can streamline production and distribution, reflecting favorably on the balance sheet. According to a white paper by the Indian Textile Ministry, "Infrastructure modernization is not just about reducing cost, but about staying relevant in competitive markets."
"The textile industry's growth in India is intrinsically linked to the infrastructural advancements we make today," says Rishabh Thakur, a leading textile economist.
Moreover, region-specific factors such as climate can indirectly play a role in determining infrastructure expenses. For instance, adequate ventilation systems in humid areas or enhanced insulation for colder regions are infrastructural elements requiring consideration. Thus, while the initial investment in infrastructure might seem extensive, its role in shaping a sustainable operation cannot be overstated, ensuring that as the industry grows, the business thrives efficiently within its chosen locale.
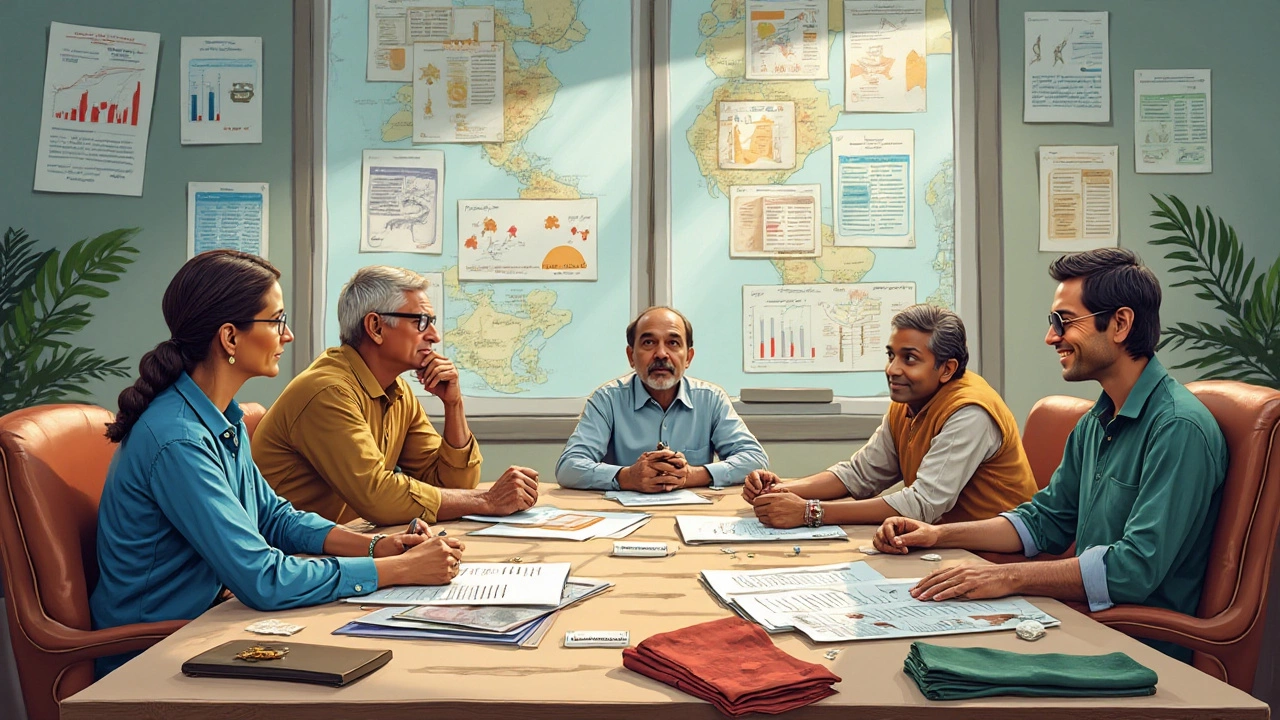
Government Schemes and Policies
Establishing a small textile manufacturing setup in India involves not just capital expenditure on tangible assets, but also an understanding of the legal and regulatory framework the government offers. The Government of India frequently rolls out various schemes to encourage investment in the India textile industry, which many entrepreneurs might find beneficial. Recognizing these avenues can significantly alter the financial blueprint of your project.
One of the most notable initiatives is the Technology Upgradation Fund Scheme (TUFS). This scheme provides credit at reduced rates for textile factories to modernize their machinery, which is often one of the most substantial expenses. By easing the interest rate burden, the government promotes technological advancement, helping companies remain globally competitive in the ever-evolving textile market. Since its inception, TUFS has been a lifeline for numerous small-scale players, enabling them to bridge the technology gap without financial strain.
Additionally, the Integrated Processing Development Scheme (IPDS) is designed to address the critical area of environmental management and infrastructure. Many textile processes are resource-intensive, demanding well-structured infrastructure to handle effluents and pollution. IPDS provides financial support for the establishment of green technology and modern effluent treatment plants, ensuring that environmental compliance becomes economically feasible for small and medium enterprises.
"Financial support and easy access to technological advancement form the backbone of a sustainable and progressive textile sector," often emphasized in industry forums by stakeholders like the Confederation of Indian Textile Industry.
The Indian government also offers subsidies under various state schemes, and benefits can vary between states based on their industrial policies. Maharashtra and Gujarat, for instance, have tailored policies for the textile sector, including capital subsidies, power tariff subsidies, and even tax exemptions, which cumulatively help reduce the initial investment involved in setting up textile manufacturing units.
Incentives for Sustainable Practices
Recently, there has been a noticeable push towards sustainable textile manufacturing practices. To motivate producers, the government has launched initiatives that reward sustainable practices. These include tax rebates for using renewable energy sources like solar, and incentives for reducing water usage, which collectively contribute to the lowering of operational costs in the long run. Adopting such eco-friendly methods can also enhance the market appeal of your products, aligning well with the global shift towards sustainability.
Navigating through these schemes involves a good deal of paperwork and understanding of regulatory norms. Entrepreneurs are advised to maintain a close dialogue with local industry bodies and government offices, as they often can provide updates and guidance on how to leverage these policies effectively. A proactive approach in engaging with these schemes often spells the difference between a thriving enterprise and a struggling one.
By utilizing these government schemes, investing in textile manufacturing costs can become more manageable, allowing small players to thrive in a highly competitive environment. Therefore, staying informed and actively participating in such schemes is crucial for anyone aspiring to make a mark in the textile industry of India.